1/2" head studs test
#41

Originally Posted by Yancy
(1) Any thoughts on this?
(2) On another note, If no one has witnessed the head studs fail or stretch, wouldn't that necessarily mean that the head studs are doing their job? )
(2) On another note, If no one has witnessed the head studs fail or stretch, wouldn't that necessarily mean that the head studs are doing their job? )
stock head bolts have more elasticity, they will actually flex and rebound
arp head studs will undergo plastic deformation..and remain deformed (they stretch and do not rebound-so when it happens one time, that's all folks

As far as your question about swapping out head studs...it can be done with the motor in the car, but would be MUCH easier with pulling the motor...
the stronger head stud idea...yes, you could torque them down slightly more...for really extreme power, you are going to want to use larger diameter studs, not just because you can apply a greater amount of torque, but also the larger diameter will provider better clamping force over a larger surface area...so even torquing a 14mm stud to 77ft lbs is better than a standard arp stud to 77ft lbs

The best combo is a 12 or 14mm studs torqued down to 105ft lbs!!! (with use of time certs of course)
#42

OverZ, the OEM head gaskets I have in front of me show quite a bit of movement across most of the cylinder bore, rather than just the bridges between them. Maybe 350zDCalb can chime in on the condition of his, as I know he just took his engine apart as well.
I am am still unclear if the cylinders are actually moving, or if the lack of adequate clamping force is causing the combustion gases to break the head gasket.
I am am still unclear if the cylinders are actually moving, or if the lack of adequate clamping force is causing the combustion gases to break the head gasket.
#43
Thread Starter
Registered User
iTrader: (27)
Joined: Sep 2004
Posts: 4,268
Likes: 1
From: tigard oregon

Originally Posted by Sharif@Forged
OverZ, the OEM head gaskets I have in front of me show quite a bit of movement across most of the cylinder bore, rather than just the bridges between them. Maybe 350zDCalb can chime in on the condition of his, as I know he just took his engine apart as well.
I am am still unclear if the cylinders are actually moving, or if the lack of adequate clamping force is causing the combustion gases to break the head gasket.
I am am still unclear if the cylinders are actually moving, or if the lack of adequate clamping force is causing the combustion gases to break the head gasket.
yes, movement looked pretty consistent. i was looking at the inner most ring going around the cylinders, and i was only missing this compound on the bridges. weird thing about it is though, i was missing more of it on the head side of the gasket than the block side. i had what appeared to be back and forth marks around the outside of the end cylinders. i need to get a microscope and look closer, but this was consistent on both head gaskets, and the marks were on the block side, not the head side.
have an easy fix for this too, lol

#44

Originally Posted by Sharif@Forged
OverZ, the OEM head gaskets I have in front of me show quite a bit of movement across most of the cylinder bore, rather than just the bridges between them. Maybe 350zDCalb can chime in on the condition of his, as I know he just took his engine apart as well.
I am am still unclear if the cylinders are actually moving, or if the lack of adequate clamping force is causing the combustion gases to break the head gasket.
I am am still unclear if the cylinders are actually moving, or if the lack of adequate clamping force is causing the combustion gases to break the head gasket.
-TODD
Last edited by 350zDCalb; 04-28-2006 at 01:17 PM.
#45

What it probably comes down to, is that upgraded studs will take people to 650-700whp, and sleeves will be required beyond that. Darton sleeves with standard ARP studs didnt start blowing gaskets until 750whp+.
#46
Thread Starter
Registered User
iTrader: (27)
Joined: Sep 2004
Posts: 4,268
Likes: 1
From: tigard oregon

as it is sounding to me with what todd saw on his gaskets and what i saw on mine, is that it is the head flexing between the head bolts. my fix takes care of one of these axises. either way, i feel the upgraded head studs is a good idea, but i don't think they are as much of a problem as originally thought. but anyone going 575rwhp or more, should definately go with the upgraded head studs, 1/2" or L-19.
my head gaskets showed a pretty uniform pattern that was not hard to read. there is also 3 dimpled rings that go around each cylinder. my main concern was the first ring sealing the cylinder. luckily with the block fix junk i put in there, it left alot of markings making my gaskets alot easier to read. still a microscope or magnifying glass will be needed for me to confirm exactly where or if i was getting movement on the cylinder tops.
my head gaskets showed a pretty uniform pattern that was not hard to read. there is also 3 dimpled rings that go around each cylinder. my main concern was the first ring sealing the cylinder. luckily with the block fix junk i put in there, it left alot of markings making my gaskets alot easier to read. still a microscope or magnifying glass will be needed for me to confirm exactly where or if i was getting movement on the cylinder tops.
#47

Originally Posted by Sharif@Forged
What it probably comes down to, is that upgraded studs will take people to 650-700whp, and sleeves will be required beyond that. Darton sleeves with standard ARP studs didnt start blowing gaskets until 750whp+.

I just got my SVRT 3 inch exhaust and w/g dump/relocation kit and electric water pump and thermostatic controller. Car should be done real soon, break in, then tune. Just waiting on my ATS triple disc clutch and flywheel, which has been held up in customs now for like a week (or atleast that's what I'm being told).
Just want to avoid the headlift issue this summer, cuz I'm thinking that since I got the sleeves I'll be punching this out to the 3.8 next winter and, if needed, can add the 1/2 studs then. Also, been thinking about looking into a half tub for the rear wheels. I wonder if (if half tubbed) we could fit a 335 out back.

#51
Thread Starter
Registered User
iTrader: (27)
Joined: Sep 2004
Posts: 4,268
Likes: 1
From: tigard oregon

didn't have time fri to locate the parts needed for this. will get it figured tomorrow and let everyone know by tomorrow night. i'm starting to think this should be stickied. this is something that can effect everyone that is f/i.
#52
Thread Starter
Registered User
iTrader: (27)
Joined: Sep 2004
Posts: 4,268
Likes: 1
From: tigard oregon

i wanted to add that since replacing my head gaskets last week i have put about 250 miles on the car so far, and once getting all the air out of the motor, i have not lost a drop yet. again, before the swap, i could only make it about 100 miles before all my water was gone, even driving like a grandma and never making it out of vacuum.
i am a pretty darn quick wrench and the swap still took me about 20 hours non-stop. i didn't even remove the exhaust manifolds or turbos or anything. i was able to lift the head and support it about 2-3" off the block and clean underneath it.
now the reason i am sharing this is to say that atleast in my situation, the heads or block were not seriously warped, creating the compromised seal of the head gasket. i got into the throttle pretty hard this weekend without loosing a drop of water, where before i would have been out of water literally a couple minutes later.
now for those of you contimplating having just your head gaskets swapped. take into account the time it takes and the labor prices. this was more of a test for me, as you should have the head and block decks atleast checked for straight. but the stock gaskets are cheap at about $30-$35 each.
i am a pretty darn quick wrench and the swap still took me about 20 hours non-stop. i didn't even remove the exhaust manifolds or turbos or anything. i was able to lift the head and support it about 2-3" off the block and clean underneath it.
now the reason i am sharing this is to say that atleast in my situation, the heads or block were not seriously warped, creating the compromised seal of the head gasket. i got into the throttle pretty hard this weekend without loosing a drop of water, where before i would have been out of water literally a couple minutes later.
now for those of you contimplating having just your head gaskets swapped. take into account the time it takes and the labor prices. this was more of a test for me, as you should have the head and block decks atleast checked for straight. but the stock gaskets are cheap at about $30-$35 each.
#53

a 14mm stud is insane, these aren't top fuel cars. if a 1/2" stud isn't can't lock the head down, you're problem lies elsewhere. a 1/2" stud can take well over 2000hp.
stock head bolts will not strech and reform. and you will not be streching 1/2" arp studs without massive detonation, enough so that you'd split the block in half first.
stock head bolts will not strech and reform. and you will not be streching 1/2" arp studs without massive detonation, enough so that you'd split the block in half first.
Originally Posted by 350zDCalb
The way it was explained to me...stock head bolts vs ARP head studs:
stock head bolts have more elasticity, they will actually flex and rebound
arp head studs will undergo plastic deformation..and remain deformed (they stretch and do not rebound-so when it happens one time, that's all folks
)
As far as your question about swapping out head studs...it can be done with the motor in the car, but would be MUCH easier with pulling the motor...
the stronger head stud idea...yes, you could torque them down slightly more...for really extreme power, you are going to want to use larger diameter studs, not just because you can apply a greater amount of torque, but also the larger diameter will provider better clamping force over a larger surface area...so even torquing a 14mm stud to 77ft lbs is better than a standard arp stud to 77ft lbs
The best combo is a 12 or 14mm studs torqued down to 105ft lbs!!! (with use of time certs of course)
stock head bolts have more elasticity, they will actually flex and rebound
arp head studs will undergo plastic deformation..and remain deformed (they stretch and do not rebound-so when it happens one time, that's all folks

As far as your question about swapping out head studs...it can be done with the motor in the car, but would be MUCH easier with pulling the motor...
the stronger head stud idea...yes, you could torque them down slightly more...for really extreme power, you are going to want to use larger diameter studs, not just because you can apply a greater amount of torque, but also the larger diameter will provider better clamping force over a larger surface area...so even torquing a 14mm stud to 77ft lbs is better than a standard arp stud to 77ft lbs

The best combo is a 12 or 14mm studs torqued down to 105ft lbs!!! (with use of time certs of course)
#54
Thread Starter
Registered User
iTrader: (27)
Joined: Sep 2004
Posts: 4,268
Likes: 1
From: tigard oregon

here is a pic showing the comparison of the stock, stock size arp, and then the 1/2" stud we are using from arp.
left to right-1/2" arp, stock size arp (ya it is missing the threads), stock head bolt
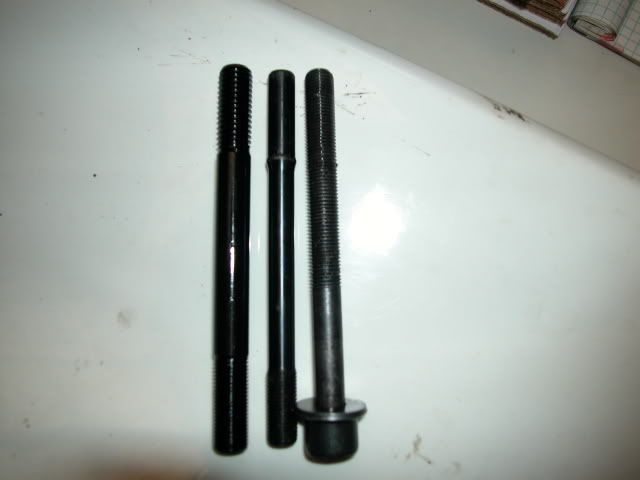
the 1/2" is now available through me at $250 a set. along with purchase will come the install instructions for the VQ35. machining costs will be around $300. again this is the same bolt i used and process for reaching over 170lbs torque (last known figure) and still managed to get another 1/4-1/2 turn on the nut, which could put the block thread test strength up around 200lbs torque. unfortunately i didn't have anything to read higher and my arms couldn't turn the torque wrench more, so we never even found the failure point. all we know is it is well past whatever can be tossed at it.
left to right-1/2" arp, stock size arp (ya it is missing the threads), stock head bolt
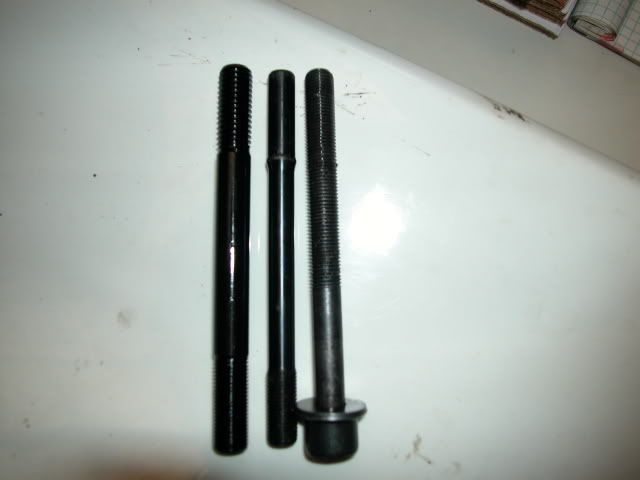
the 1/2" is now available through me at $250 a set. along with purchase will come the install instructions for the VQ35. machining costs will be around $300. again this is the same bolt i used and process for reaching over 170lbs torque (last known figure) and still managed to get another 1/4-1/2 turn on the nut, which could put the block thread test strength up around 200lbs torque. unfortunately i didn't have anything to read higher and my arms couldn't turn the torque wrench more, so we never even found the failure point. all we know is it is well past whatever can be tossed at it.
#55
Thread Starter
Registered User
iTrader: (27)
Joined: Sep 2004
Posts: 4,268
Likes: 1
From: tigard oregon

searching the country right now for the correct parts needed to complete and package the other fix i have found. should know by the end of day which way i need to go to package this in an easy diy kit.
#56

Originally Posted by overZealous1
searching the country right now for the correct parts needed to complete and package the other fix i have found. should know by the end of day which way i need to go to package this in an easy diy kit.
#57
Thread Starter
Registered User
iTrader: (27)
Joined: Sep 2004
Posts: 4,268
Likes: 1
From: tigard oregon

Originally Posted by booger
Any news you can share ?
my main concern is to keep this a relatively cheap mod, and at the same time very effective. i know those are words most of us are not used to in the f/i 350Z forum

i will be posting another thread about it once it is sorted out. i feel everyone should be familiar with this mod and everyone, built motor or not, will benefit from it. heck, this can be done in the car with regular hand tools in a couple hours, even if your slow!!

#58

You got me now !!!! I thought it was going to be something to do with the head gaskets . I couldnt amagine what it could be to help with the head lifting problem . And only take a couple hours .
#59
Thread Starter
Registered User
iTrader: (27)
Joined: Sep 2004
Posts: 4,268
Likes: 1
From: tigard oregon

Originally Posted by booger
You got me now !!!! I thought it was going to be something to do with the head gaskets . I couldnt amagine what it could be to help with the head lifting problem . And only take a couple hours .
lol.

#60

Originally Posted by royce so
a 14mm stud is insane, these aren't top fuel cars. if a 1/2" stud isn't can't lock the head down, you're problem lies elsewhere. a 1/2" stud can take well over 2000hp.
stock head bolts will not strech and reform. and you will not be streching 1/2" arp studs without massive detonation, enough so that you'd split the block in half first.
stock head bolts will not strech and reform. and you will not be streching 1/2" arp studs without massive detonation, enough so that you'd split the block in half first.
Royce so..not sure if you meant to agree with me or you were saying that the stock head studs do not deform..this is not my opinion

the stock head bolts are designed to be able to flex and reform a bit..Talk with some of the engineers at ARP and they will explain how the arp studs differ from stock, in that they do not rebound

12mm should suffice for high power, but I am using 14mm in my motor..I'm sure this is overkill, but that is the way I roll

also, your claim of how a 12mm stud can take over 2000hp..this is a generalization you can't make regarding all motors...the head stud pattern differs from motor to motor...the vq head utilizes 8 studs holding it to the block...the location of the studs isn't as beneficial in overall clamping force as say some american motors (that may have 3 studs surrounding each cylinder). The larger the stud, the more surface area that it will cover (and clamp)- the greater it will uniformly hold the head... we are limited at how large we can go with the head studs, because we begin to run out of material in the block to surround the stud

We will offer a 12mm head stud upgrade, with use of time certs (these will allow the larger stud to clamp into a larger surface area--reducing any chance of stripping out of the aluminum block (again, probably overkill for torquing to 95-100ft lbs..but also an extra safety measure to prevent pulling your motor out later than sooner

-TODD
Last edited by 350zDCalb; 05-01-2006 at 08:57 PM.