TrackPack's Turbo Fab Thread...
#21

No need to ask what that is.. we all know.. great work for your first try, i remember trying out my first 4-1 collector for my SR manifold.. didnt come out half as nice as that.
you have some nice cutting/welding skills... what kind of Tig do you have?
you have some nice cutting/welding skills... what kind of Tig do you have?
#22
Thread Starter
Registered User
iTrader: (1)
Joined: Nov 2006
Posts: 143
Likes: 0
From: Winnipeg, Mb, Canada

Originally Posted by Doba
No need to ask what that is.. we all know.. great work for your first try, i remember trying out my first 4-1 collector for my SR manifold.. didnt come out half as nice as that.
you have some nice cutting/welding skills... what kind of Tig do you have?
you have some nice cutting/welding skills... what kind of Tig do you have?

Me and Brad both own Miller 180sd's, great little machines.
With collectors, you need some sort of jig so that you can replicate every cut, makes them alot quicker and more accurate.
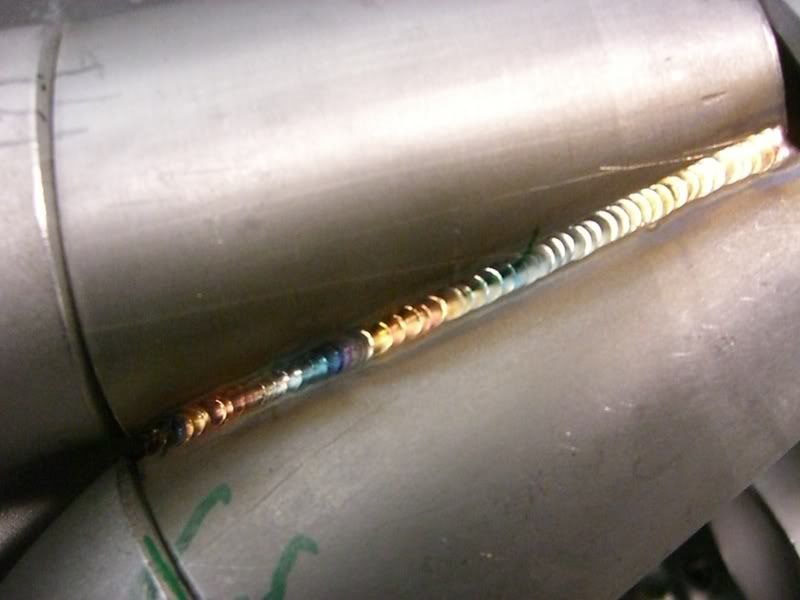
Theres some collector welding by Brad, he's a wizard with the torch.

#24
Thread Starter
Registered User
iTrader: (1)
Joined: Nov 2006
Posts: 143
Likes: 0
From: Winnipeg, Mb, Canada

Hey guys, have another pic or 2 here for you, hope you like.
Tacked up manifold...
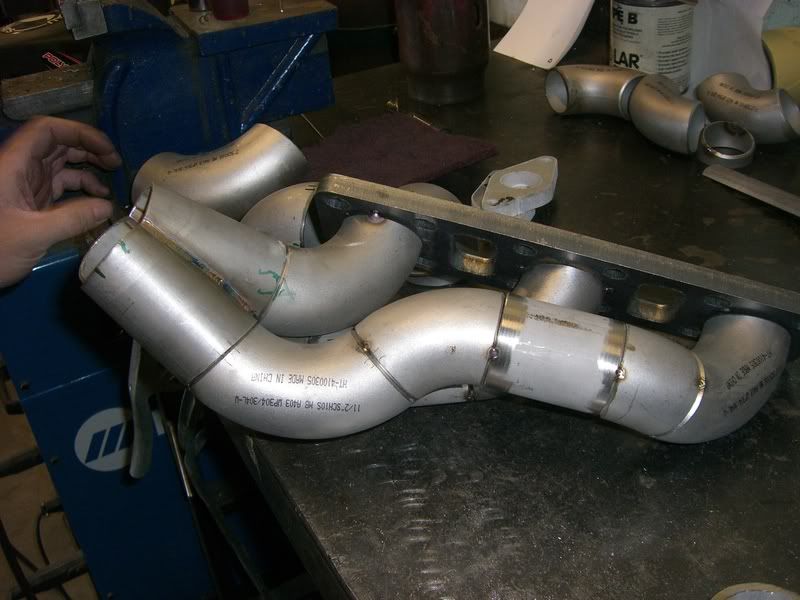
The collector again.
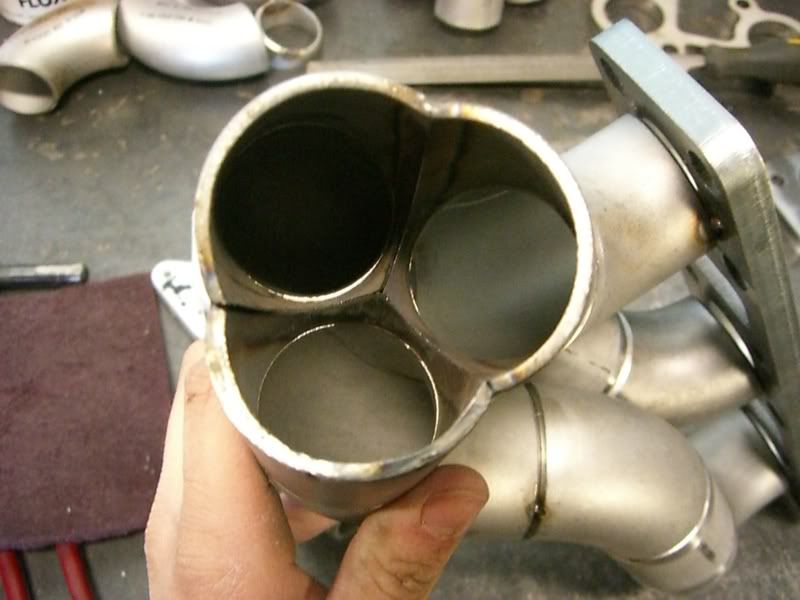
cut.....tack.......cut......tack......grind.....cut......tac k..........
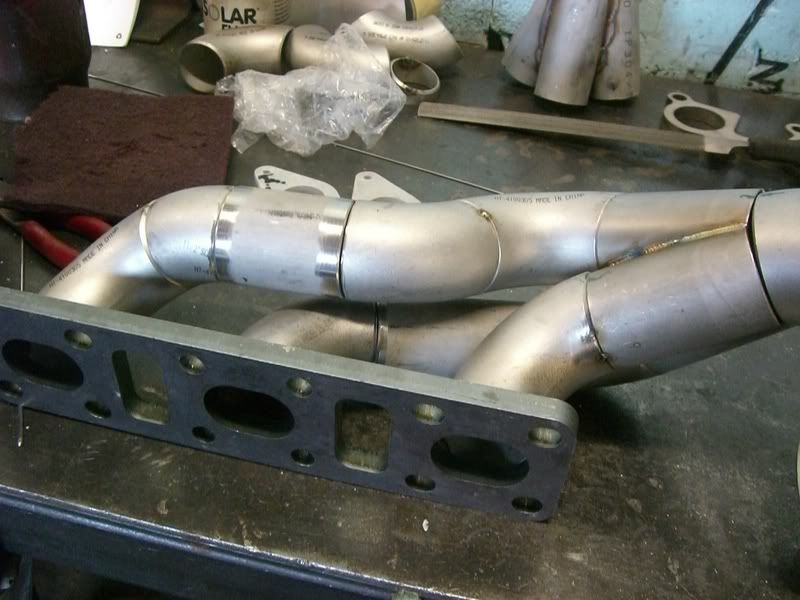
quick test fit.....
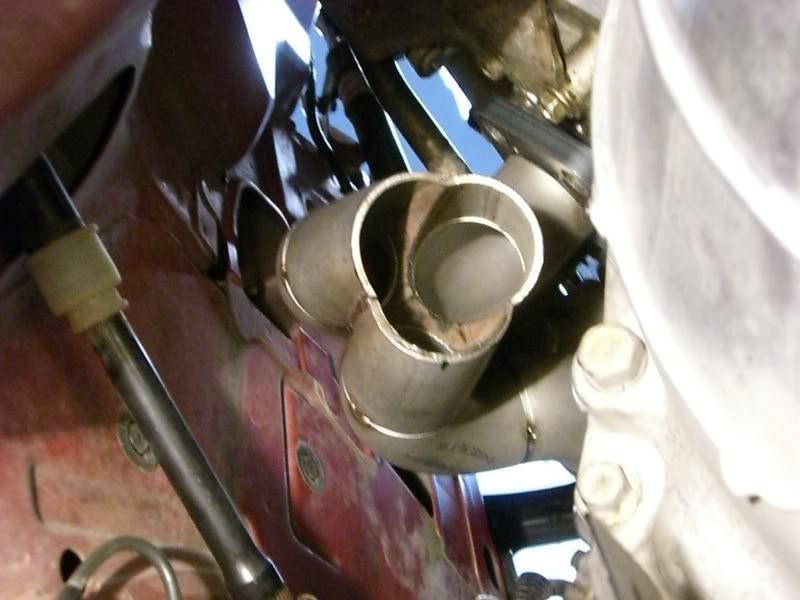
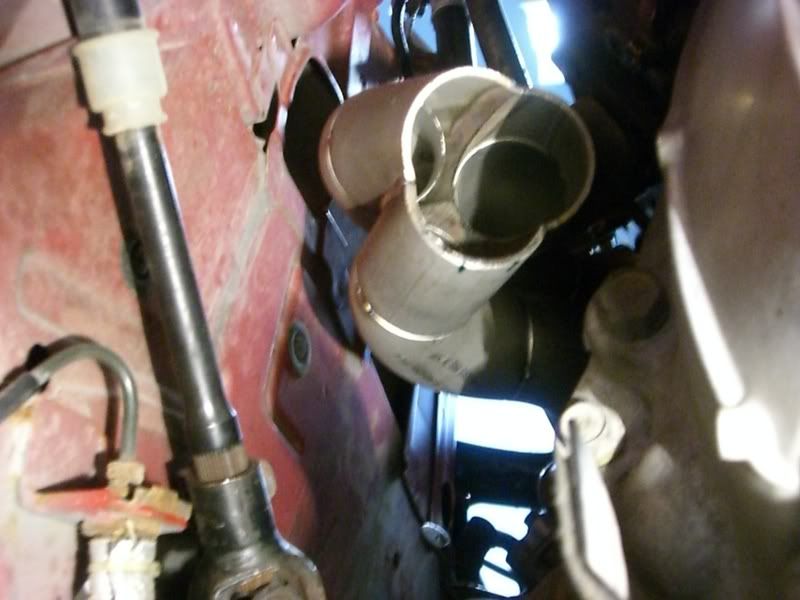
leave you guys with those for now, if you have any questions ask away!
Tacked up manifold...
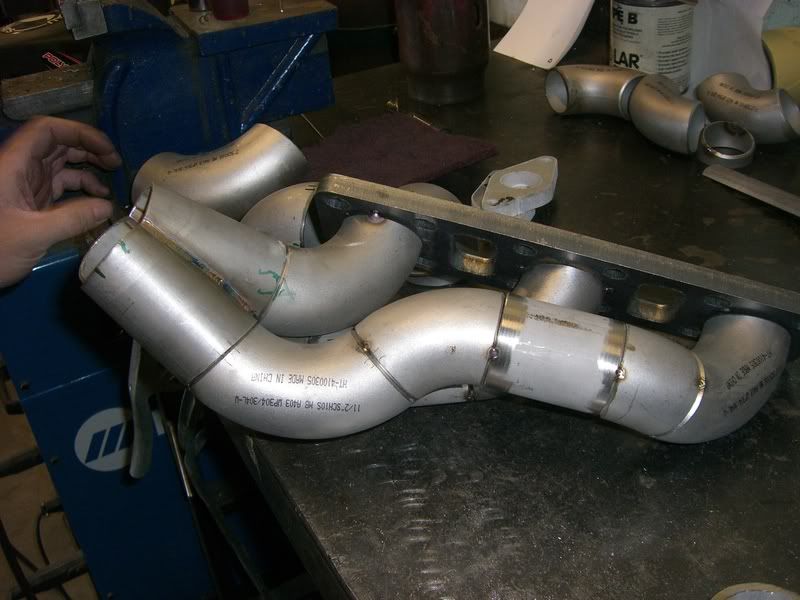
The collector again.
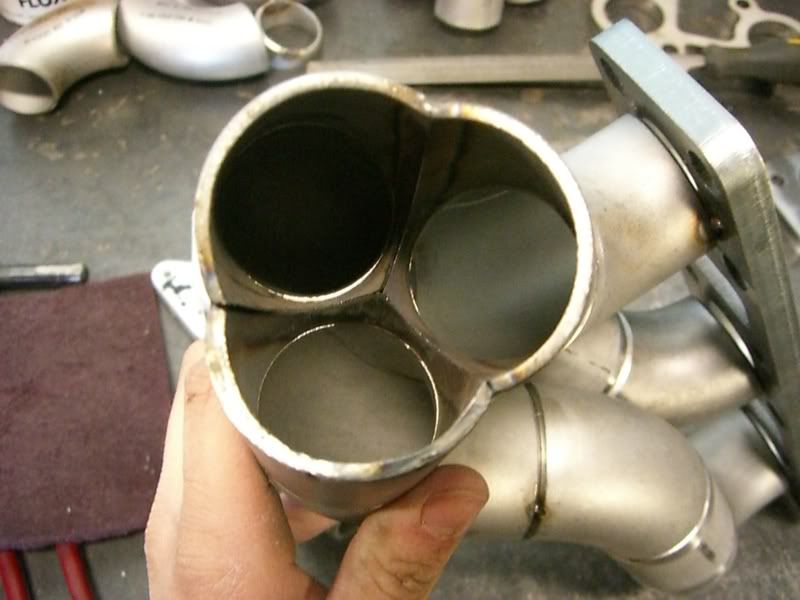
cut.....tack.......cut......tack......grind.....cut......tac k..........
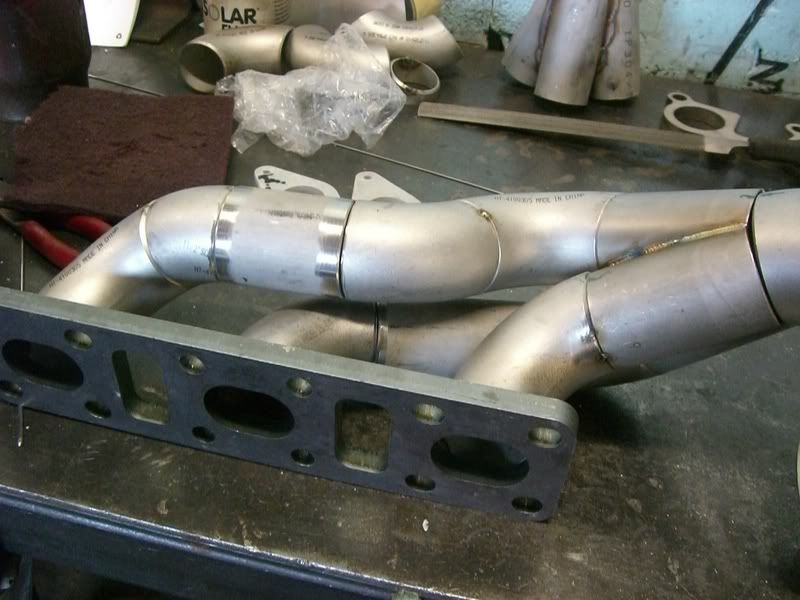
quick test fit.....
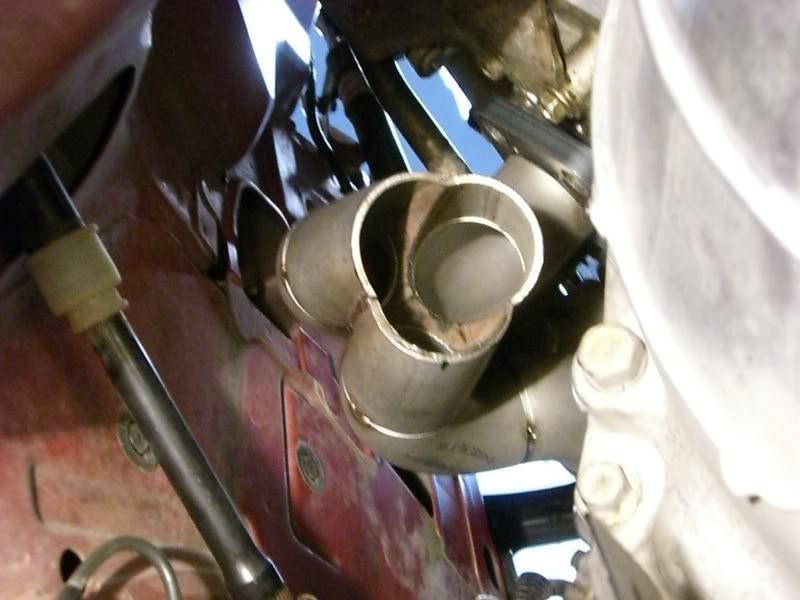
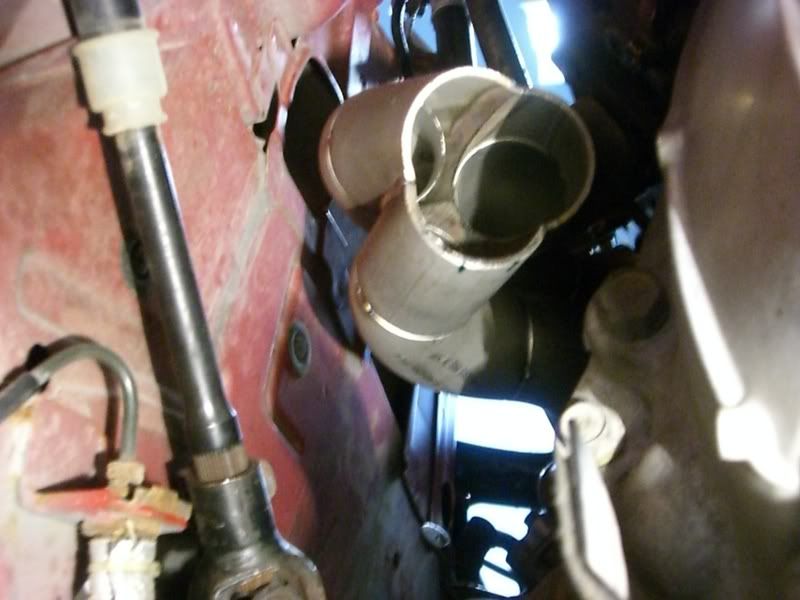
leave you guys with those for now, if you have any questions ask away!
#27
Thread Starter
Registered User
iTrader: (1)
Joined: Nov 2006
Posts: 143
Likes: 0
From: Winnipeg, Mb, Canada

The header material is still 304 but its classified as pipe and not tube, generally headers are 1.9mm/.074" tube which is actually pretty weak(think ssautocrome...) and gets very weak in the heat affected zones,you'll notice that stuff like the ssautocrome will fail right beside the weld because the material was weakened in the welding process.
This stuff is 2.77mm/.109" pipe, much much stronger! nuke proof! Have never seen pipe fail, consider it a life time warranty.
Here's the header getting welded
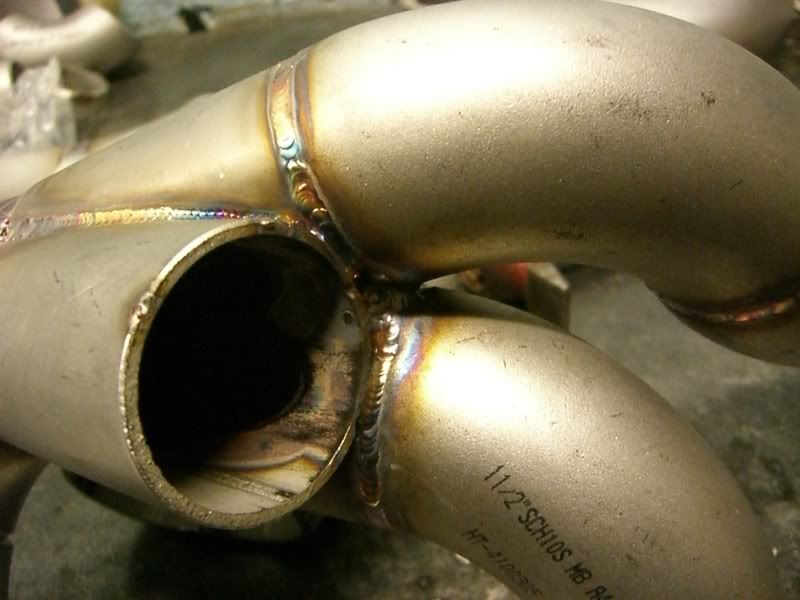
later guys!
This stuff is 2.77mm/.109" pipe, much much stronger! nuke proof! Have never seen pipe fail, consider it a life time warranty.
Here's the header getting welded

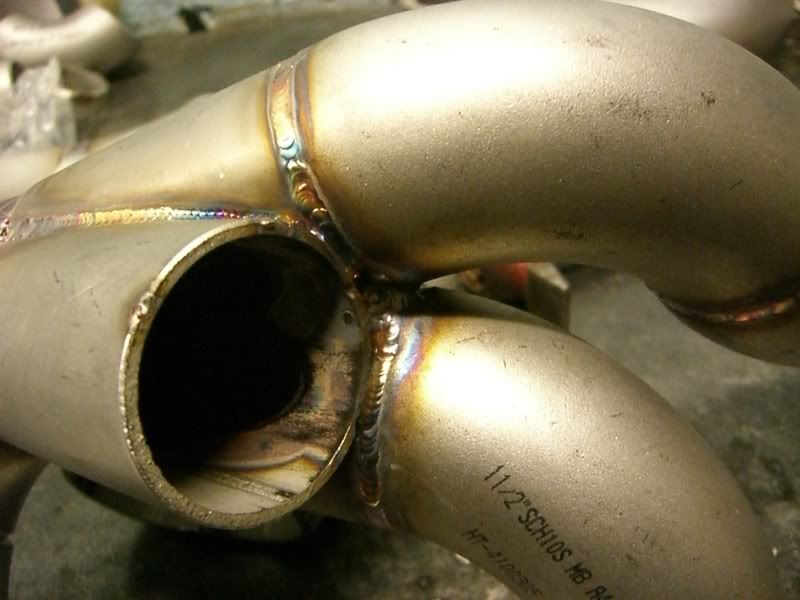
later guys!
#30
Thread Starter
Registered User
iTrader: (1)
Joined: Nov 2006
Posts: 143
Likes: 0
From: Winnipeg, Mb, Canada

Originally Posted by QuadCam
where did you get the exhaust manifold flange for our heads? spdexhaust.com?
Thanks again for the kind words guys!
I'll keep you updated.
#31

Originally Posted by TrackPack
All the flanges used on this project and cut local, very convenient to have local water jet/ laser access. I can even get exhaust gaskets cut out of copper, which I might do for the head to prevent any chance of an exhaust leak.
Thanks again for the kind words guys!
I'll keep you updated.
Thanks again for the kind words guys!
I'll keep you updated.
that's a nice convenience! copper gaskets are great...nice and soft.
#32
Thread Starter
Registered User
iTrader: (1)
Joined: Nov 2006
Posts: 143
Likes: 0
From: Winnipeg, Mb, Canada

well guys I have a few more updates, progress is slowing down these days, sooo much work to do still.
Well you know how I mentioned I had the Ross machine rails with delphi/precision injectors?......well turns out there was a fitment issue with the stock manifold...and well I wasnt about to add a spacer, guys argue on here about the 287 manifold vs the revup all the time(inch tops runner length diff?) and it seems proven that the shorter runner revup provides more top end, well a plenum spacer would only increase the already long 287 manifold......
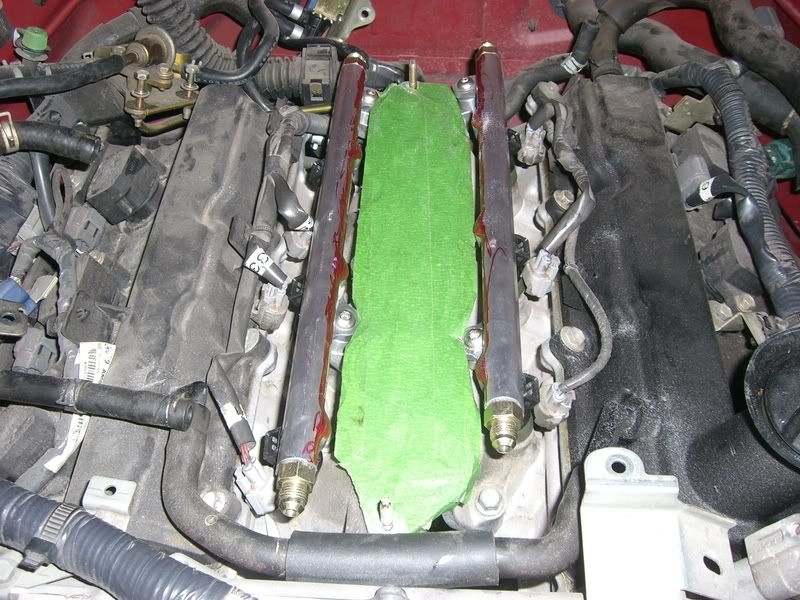
So I checked to see where it was rubbing and I thought what the hell, I could make this fit.........
Well after grinding for a while I seen some pitting in the cast, ...what is that......poked at it and my finger went right threw lol!

Ohh crap,well time to fix it.....
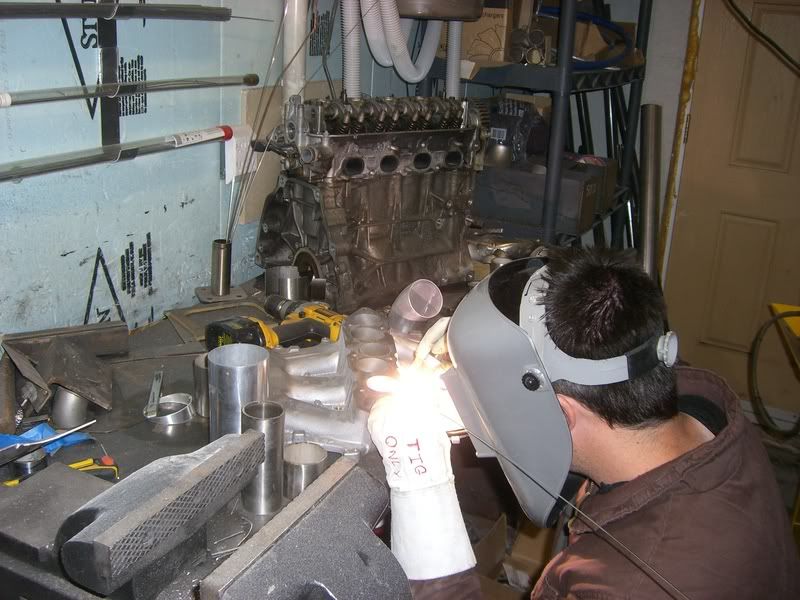
So what was the end result? well it can be done, the manifold is on flat, no spacer. Was it worth it?? well.....I'm happy that I could do it, was over a hour to 2 worth or grinding and test fitting... Would I recommend trying it............
Just get the spacer!!
Heres a welded manifold test fit...
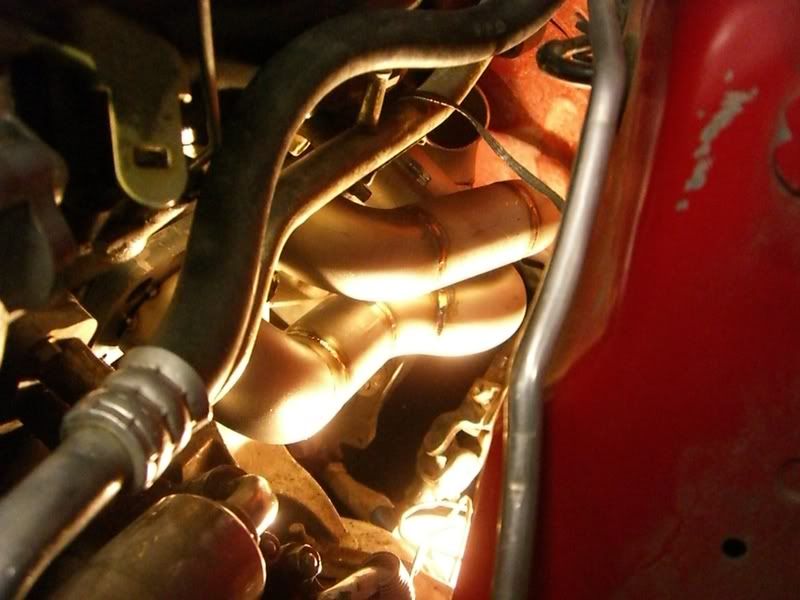
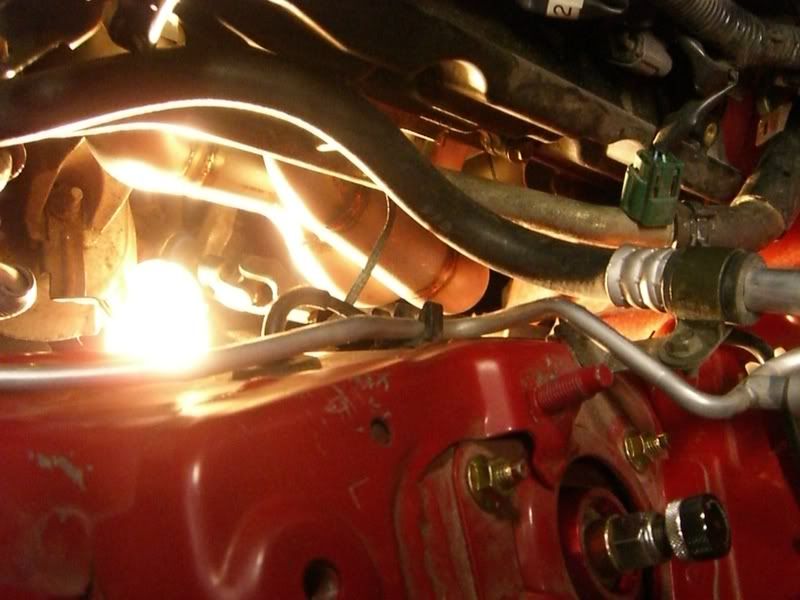
Later guys.
Well you know how I mentioned I had the Ross machine rails with delphi/precision injectors?......well turns out there was a fitment issue with the stock manifold...and well I wasnt about to add a spacer, guys argue on here about the 287 manifold vs the revup all the time(inch tops runner length diff?) and it seems proven that the shorter runner revup provides more top end, well a plenum spacer would only increase the already long 287 manifold......
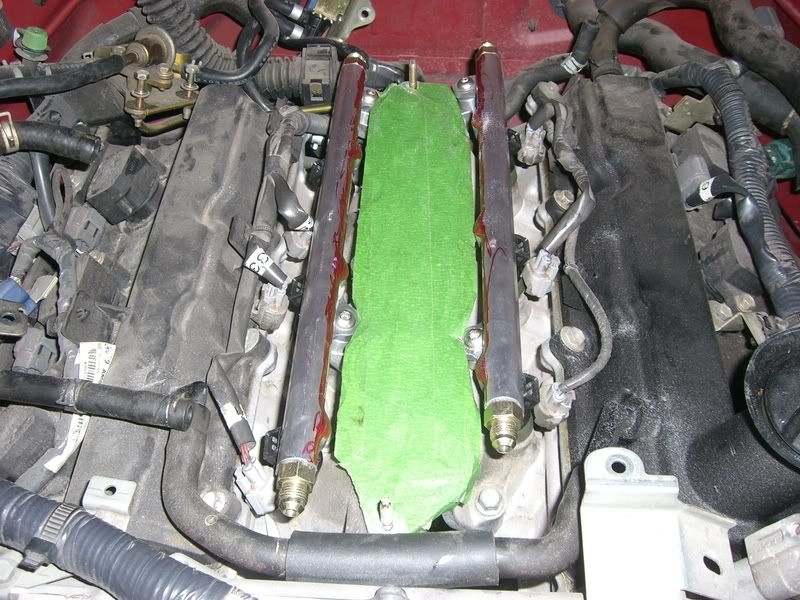
So I checked to see where it was rubbing and I thought what the hell, I could make this fit.........

Well after grinding for a while I seen some pitting in the cast, ...what is that......poked at it and my finger went right threw lol!


Ohh crap,well time to fix it.....
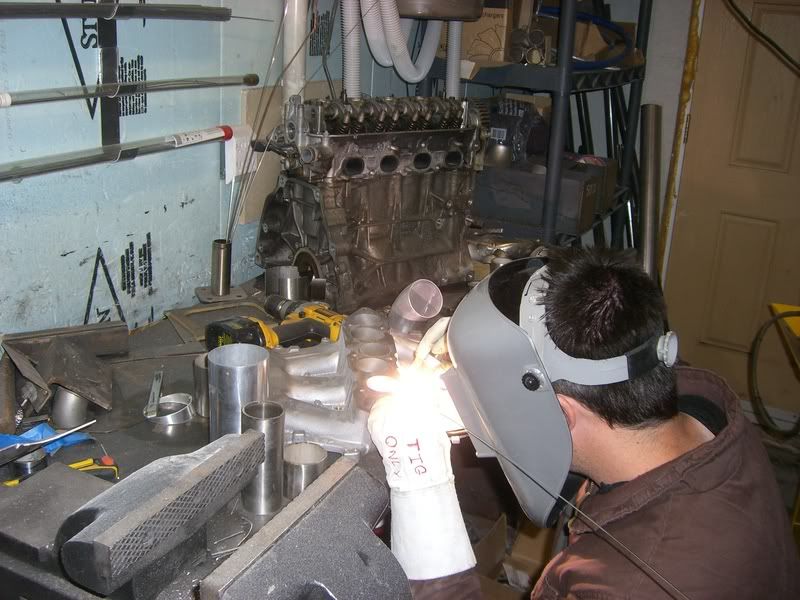
So what was the end result? well it can be done, the manifold is on flat, no spacer. Was it worth it?? well.....I'm happy that I could do it, was over a hour to 2 worth or grinding and test fitting... Would I recommend trying it............
Just get the spacer!!

Heres a welded manifold test fit...
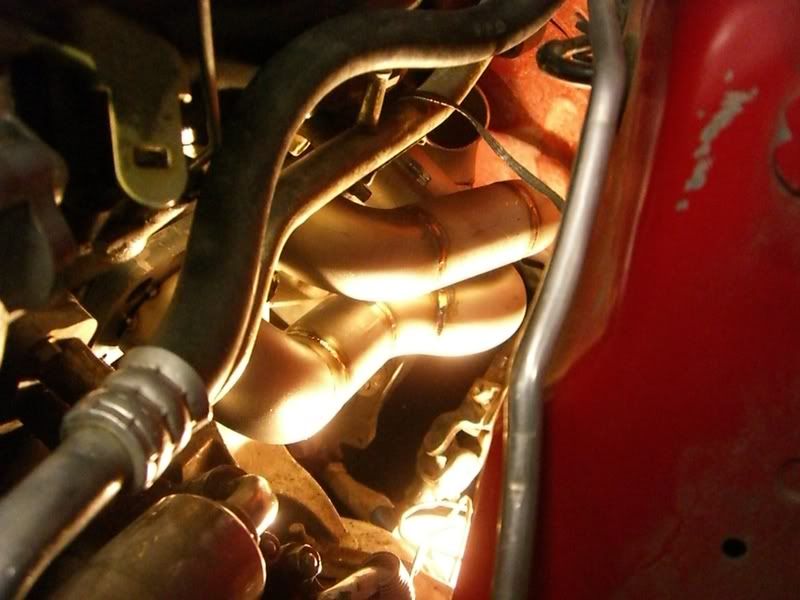
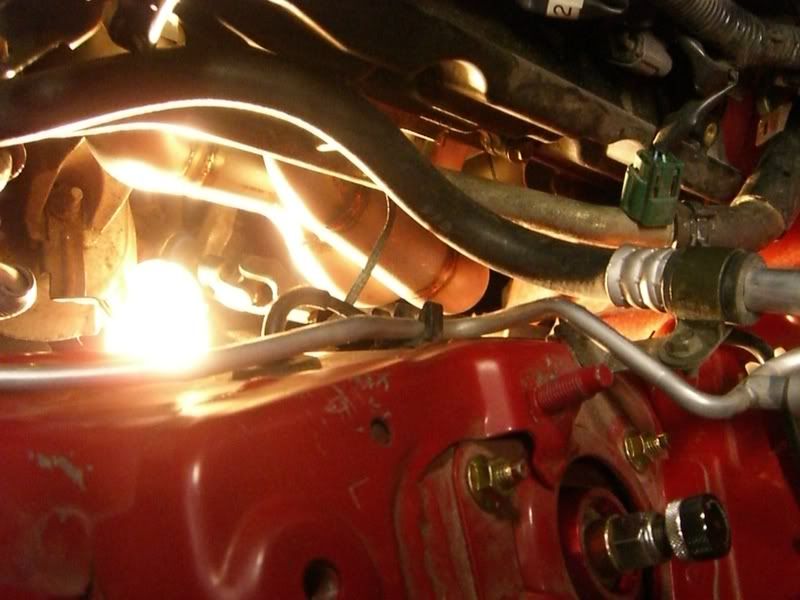
Later guys.
#37
Thread Starter
Registered User
iTrader: (1)
Joined: Nov 2006
Posts: 143
Likes: 0
From: Winnipeg, Mb, Canada

Originally Posted by QuadCam
How hard is it to self teach yourself to Tig weld? Always wanted to learn, but never have. Also, any recommendations on a good machine? Lincoln? clarke? etc?
I dont want to discourage you buy saying that it isnt easy to learn on your own,but realistically if someone gives you pointers you'll be laying beads in a week. But it takes years to truly master. Ive seen shops sell products that are reputable and people love them, but when you really critique the welds they look overheated and amateur. It really takes dedication to perfect, but to be ok isnt to hard

as for machines, me and my budy have miller 180sd's I know of a shop with a miller 200sd(250 maybe??) everyone seems pretty happy, one of those millers is a true work horse, used everyday for many years.
Ive been told its a "ford vs. chevy" argument between miller and lincoln and I have met people that say lincoln is better.
sorry man thats all the input I have on that topic...
Again thanks guys for the complements, I think your really gonna like this one...

#38
Thread Starter
Registered User
iTrader: (1)
Joined: Nov 2006
Posts: 143
Likes: 0
From: Winnipeg, Mb, Canada

Well guys, this is the updated I was holding out on.
I dont know what you'll think of it, I personally love it!
.....well this feels like dropping my pants in front of the cheerleaders...here goes nothing....

where the heck is that going...hmmm..
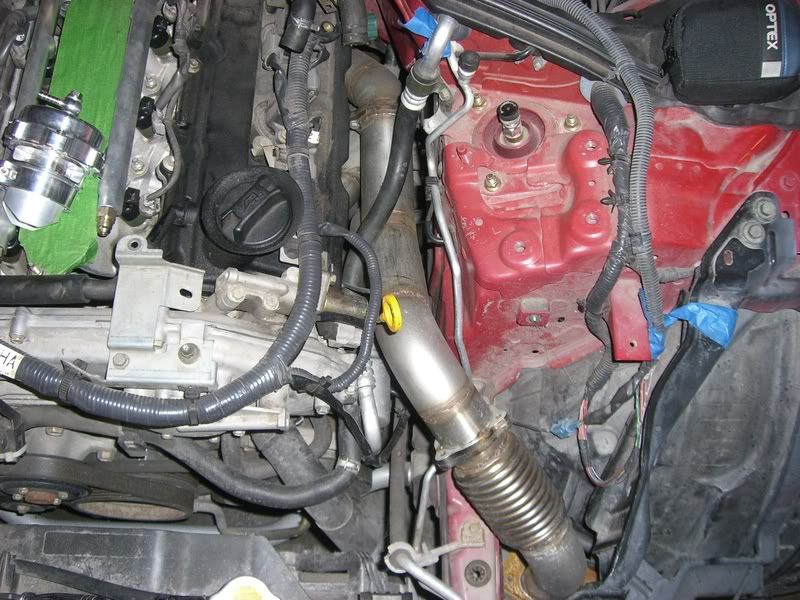
OHHH check out my new laptop!
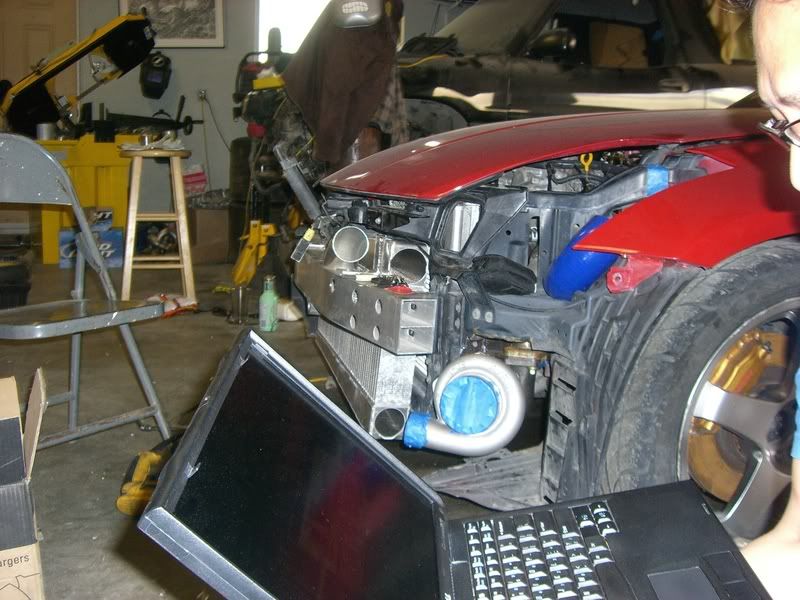
Well guys, what do you think?
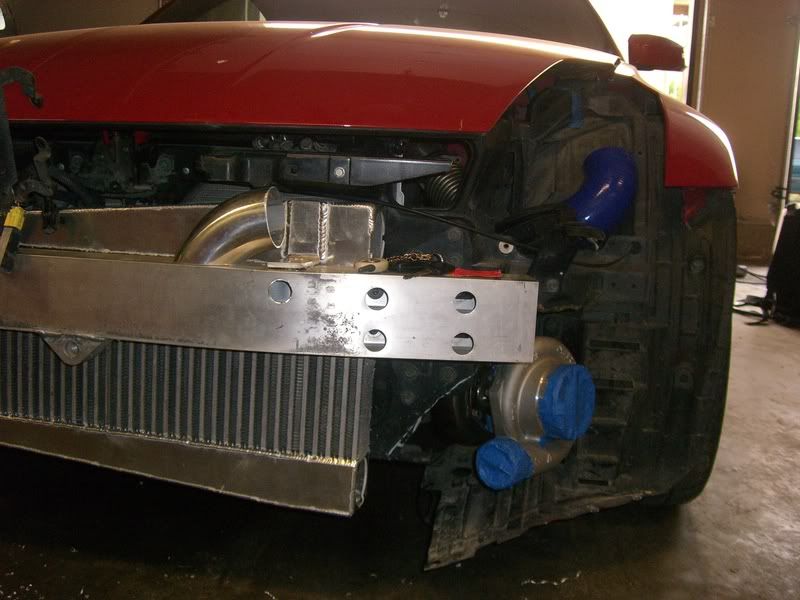
more to come soon, I'm surprised no one ever asked where the turbo would be placed lol, well let me know what you think!
I dont know what you'll think of it, I personally love it!
.....well this feels like dropping my pants in front of the cheerleaders...here goes nothing....


where the heck is that going...hmmm..
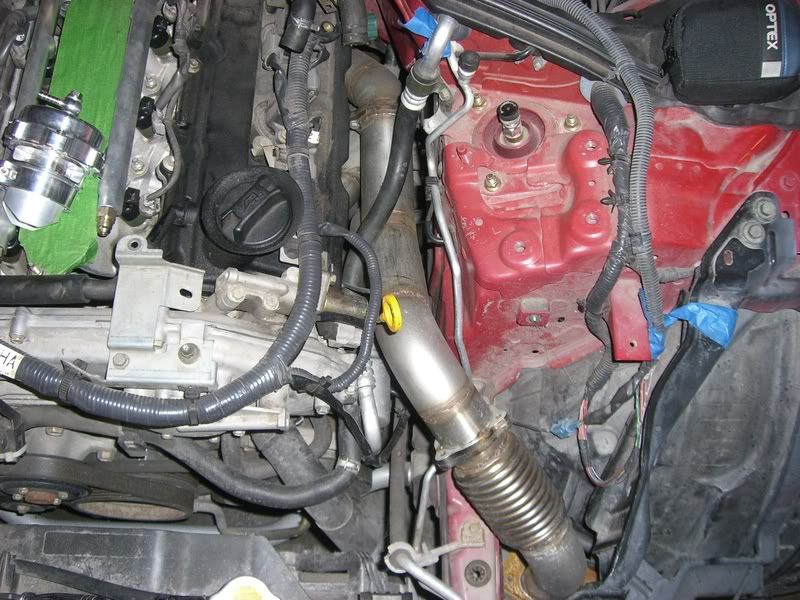
OHHH check out my new laptop!

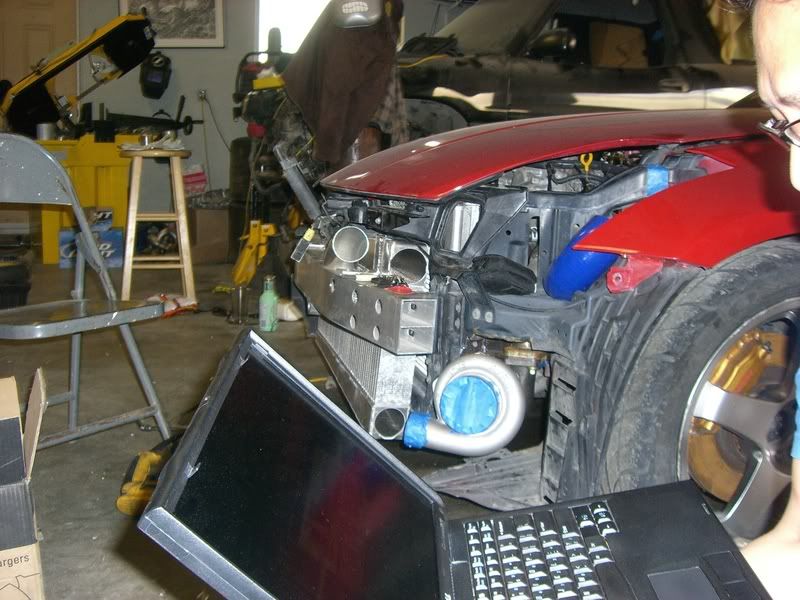
Well guys, what do you think?
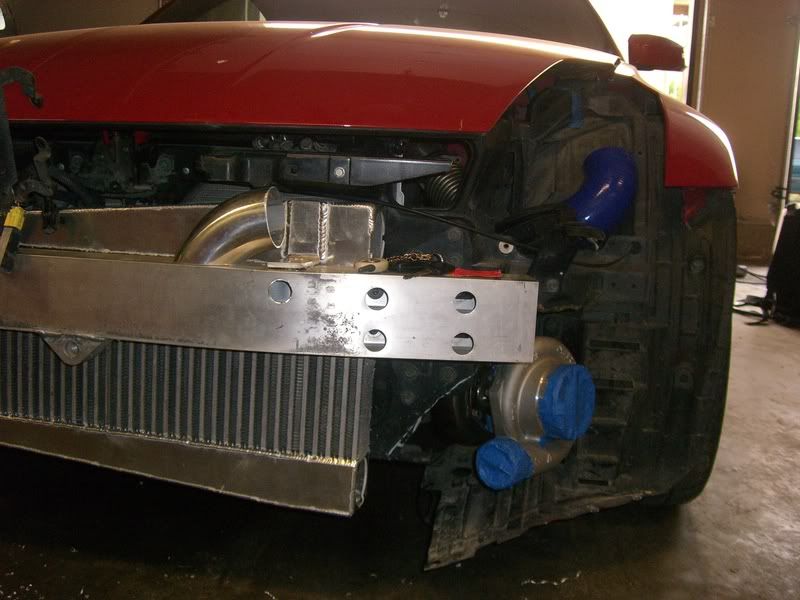
more to come soon, I'm surprised no one ever asked where the turbo would be placed lol, well let me know what you think!
#40

Originally Posted by QuadCam
How hard is it to self teach yourself to Tig weld? Always wanted to learn, but never have. Also, any recommendations on a good machine? Lincoln? clarke? etc?