No, I'm not going to turbocharge it... My TT G35.
#61
New Member
Thread Starter
iTrader: (7)
Join Date: Apr 2007
Location: York County, Pennsylvania.
Posts: 211
Likes: 0
Received 0 Likes
on
0 Posts

I see what you did there!
Small update. I don't really have pictures because I didn't feel like taking them during the process.
About 3 weeks ago I had the car on a dyno, it did an honest 500WHP at 15psi dropping off to 13psi. I tried and tried but I could not get it to make any more boost.
Discouraged I decided to try to switch the HKS exhaust out and get my hands on an APS TD 3" exhaust, and add the APS 3.5" downpipes with the idea that freeing up the exhaust would allow me more wiggle room with the internal gates.
Wouldn't you know that danisr1 had an APS TD 3" exhaust for sale here for a 350Z, a quick cut here, and measure there with some tig welding thrown in for good measure, I modified it to fit the G. Little did I know Ryan was such a salesman, and his misfortune resulted in a weekend project for me. I picked up what was left of his APS Extreme TT kit from his parted out car.
So I swapped the manifolds, turbos, downpipes, and exhaust. Then added the APS Fuel system. A quick change on the K fuel multiplier and a rescale of the load index in Osiris and I was off.
The new turbos take a bit to light off, but I can tell, even only at 11-12psi that the top end has improved, big time.
The car also sounds like it means business now. No more riding in quiet with the windows up.
I guess I'll spend some time tuning this thing and turning the boost up this week. We'll see what happens.
Small update. I don't really have pictures because I didn't feel like taking them during the process.
About 3 weeks ago I had the car on a dyno, it did an honest 500WHP at 15psi dropping off to 13psi. I tried and tried but I could not get it to make any more boost.
Discouraged I decided to try to switch the HKS exhaust out and get my hands on an APS TD 3" exhaust, and add the APS 3.5" downpipes with the idea that freeing up the exhaust would allow me more wiggle room with the internal gates.
Wouldn't you know that danisr1 had an APS TD 3" exhaust for sale here for a 350Z, a quick cut here, and measure there with some tig welding thrown in for good measure, I modified it to fit the G. Little did I know Ryan was such a salesman, and his misfortune resulted in a weekend project for me. I picked up what was left of his APS Extreme TT kit from his parted out car.
So I swapped the manifolds, turbos, downpipes, and exhaust. Then added the APS Fuel system. A quick change on the K fuel multiplier and a rescale of the load index in Osiris and I was off.
The new turbos take a bit to light off, but I can tell, even only at 11-12psi that the top end has improved, big time.
The car also sounds like it means business now. No more riding in quiet with the windows up.
I guess I'll spend some time tuning this thing and turning the boost up this week. We'll see what happens.
#63
Registered User
Join Date: Apr 2008
Location: Lancaster, PA
Posts: 39
Likes: 0
Received 0 Likes
on
0 Posts

The new exhaust sounds great Jesse. Definitely loud when you were leaving my neighborhood tonight lol. On the highway when you got on it, it had a nice healthy sound, reminiscent of an inline 6 (think RB26 or 2JZ), but with a little bit deeper growl, probably thanks to the extra displacement compared to those motors.
#64
New Member
Thread Starter
iTrader: (7)
Join Date: Apr 2007
Location: York County, Pennsylvania.
Posts: 211
Likes: 0
Received 0 Likes
on
0 Posts

I got the Boost-A-Spark installed on the silver car tonight, here is a quick how to if anyone ever wants to emulate it.
If you recall, I rewired the car last summer when I suspected weak spark causing a high RPM misfire at 16psi. Link, see post 48. That seemed to take care of the issue at the time. Now, with larger turbochargers and higher boost, the issue seems to have come back. I had tried different plugs and closing the spark plug gap up with only slight improvements.
The Boost-A-Spark is basically a voltage amplifier that takes whatever input voltage is, and increases it to whatever it is set to from 13.5V to 20V, adjustable via a control ****. This will push more voltage to the coils and in turn fire the plugs with more voltage. The unit can be active all the time by permanently connecting the trigger wires, or it can be activated at 4psi of boost using the supplied hobbs switch. I chose to use the switch and not run the higher voltage to the coils all the time.
You'll see in the link I mention that the wiring was sorted out. I had run a power feed for each coil and each IVTC solenoid to a junction behind the battery in case I needed to seperate the circuits at a later time. I decided this was the best way to accomplish this as if you just wire the BAS in series as the instructions depict, it would also be sending the higher voltage to the IVTC solenoids, I was not comfortable with that.
So I went back and seperated the 2 IVTC solenoid power wires, the 6 coil power wires, and the feed.
Now the next issue. This unit has a 10ga. power feed wire and a 30 amp fuse, to create a higher voltage, this thing needs some current flow. Once again if connected as the instructions depict, it would be connected to a tiny 14ga. (which might even be 16ga.) wire that has a 15 amp fuse protecting it. I decided to use the factory ignition wire that is also powering the IVTC solenoids to close a relay and connect the positive lead of the Boost-A-Spark directly to the battery through its fuse, of course.
All said and done it seems to work. Using my Fluke meter I set the output to 16V and went for a test drive.
It's in the 30's outside, so traction was non-existant and I can't tell if it's breaking up anymore or not as I can't load the thing down. Maybe tomorrow I can get a better test.
Here are a few pictures.
Here is the unit and what it comes with, the control ****, hobbs switch, wiring, and a few other odds and ends.
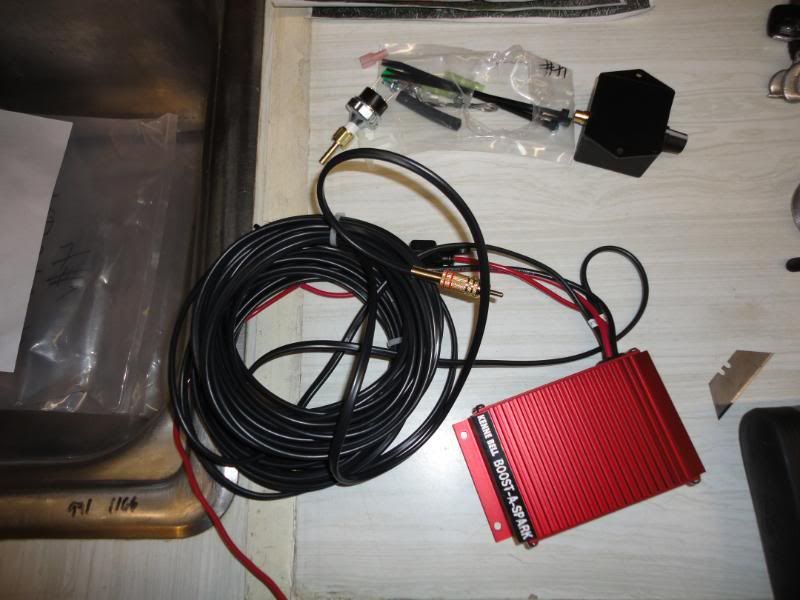
Under the hood before the install.
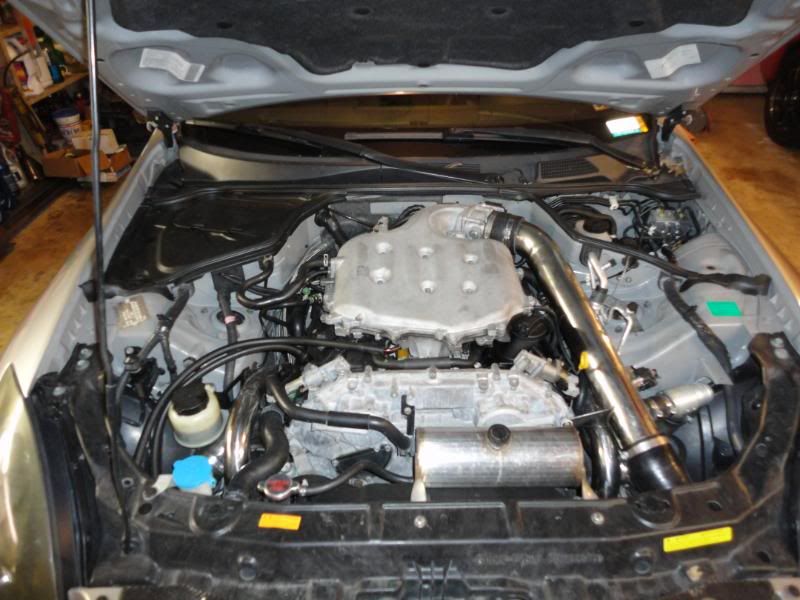
Removing the battery and such.
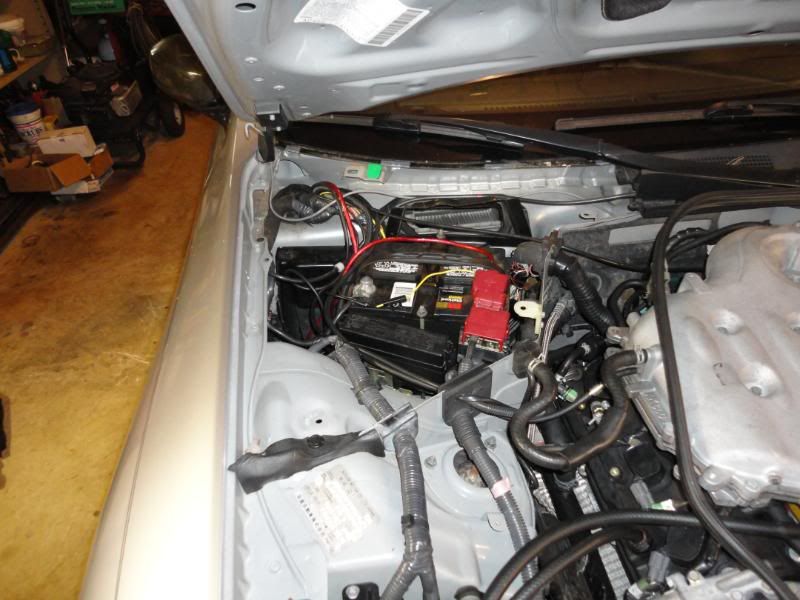
Seperating the coil and IVTC circuits.
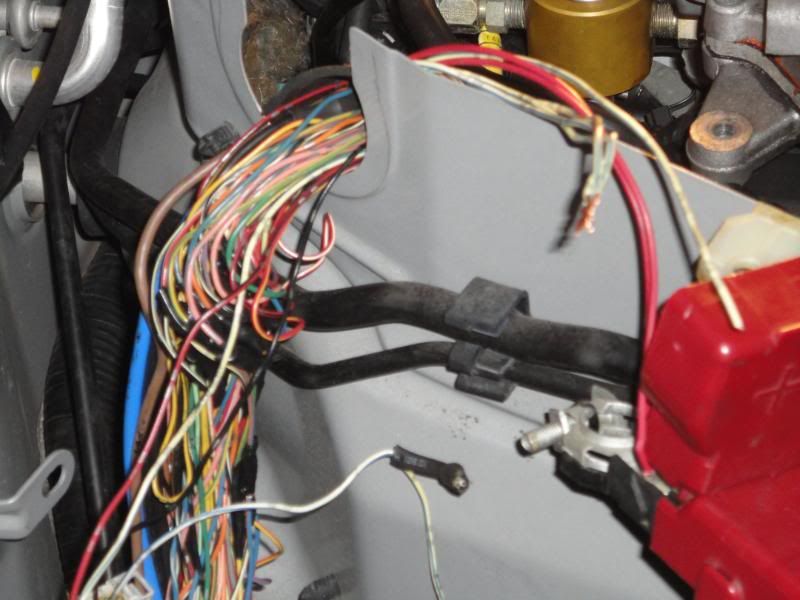
Adding the relay circuit to the BAS.
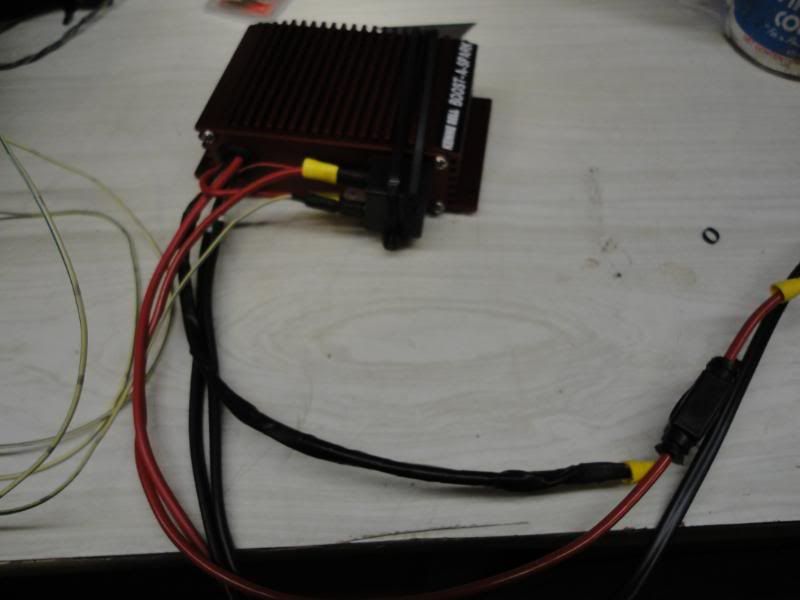
Location of the BAS.
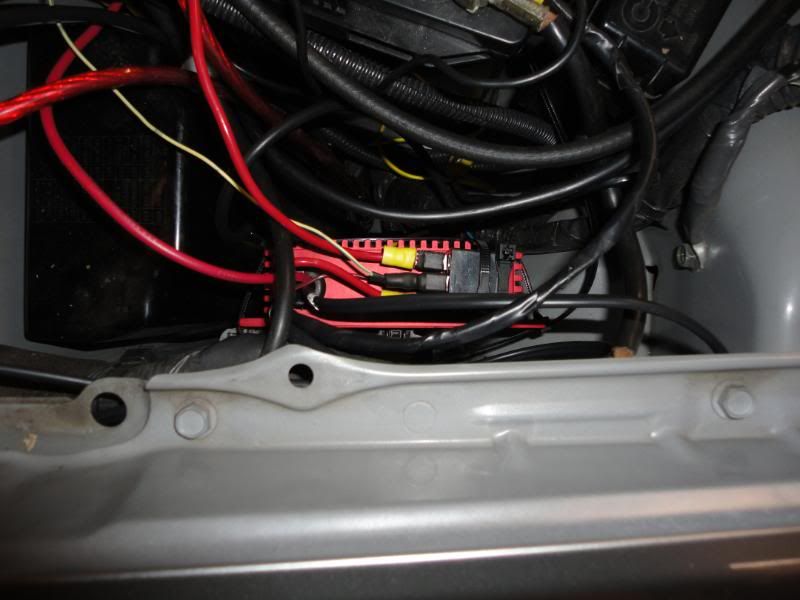
The red car got jealous, it's such an attention *****.
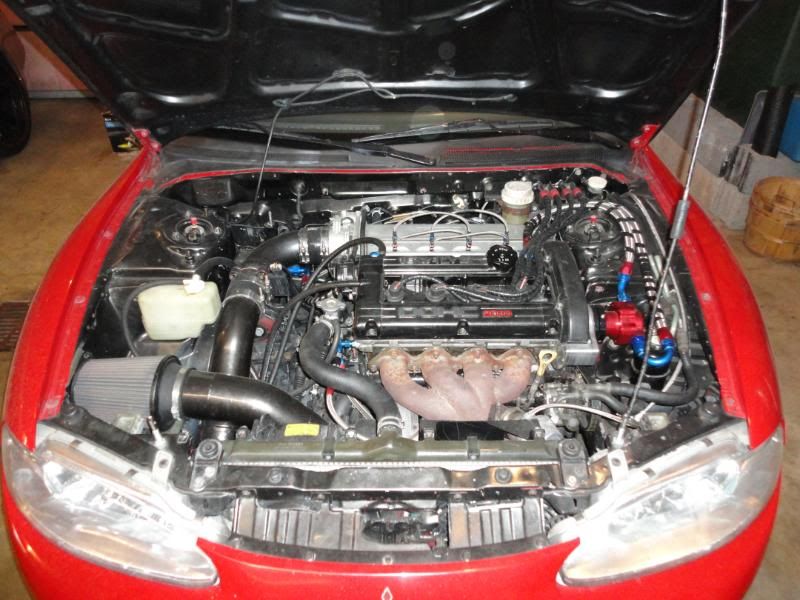
Buttoning it up.
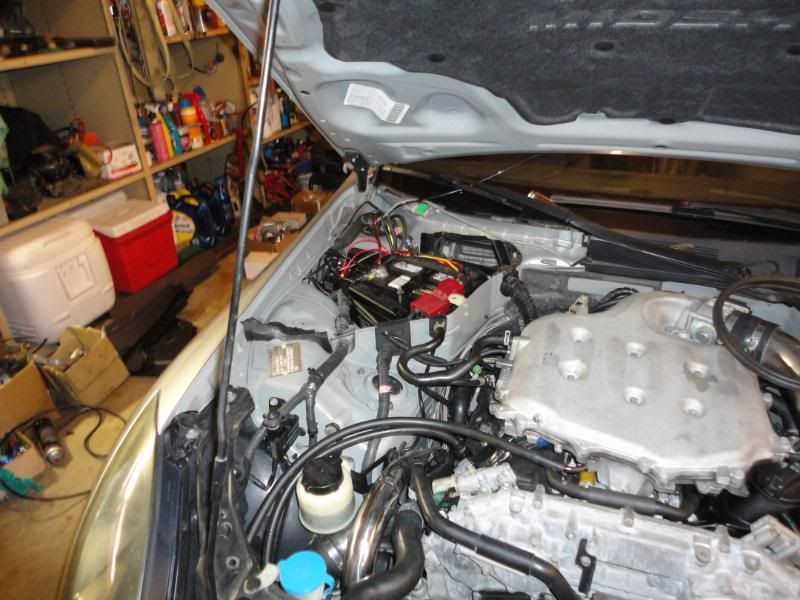
Finished.
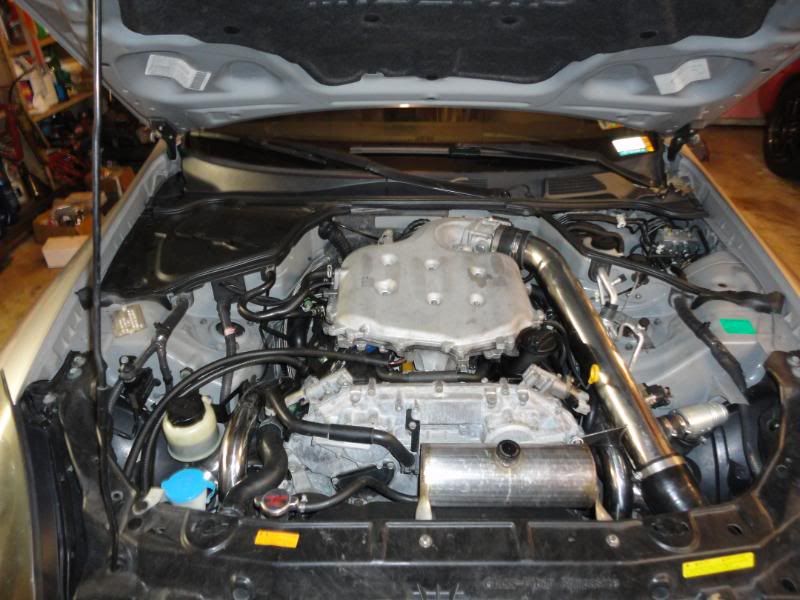
The adjustment ****.
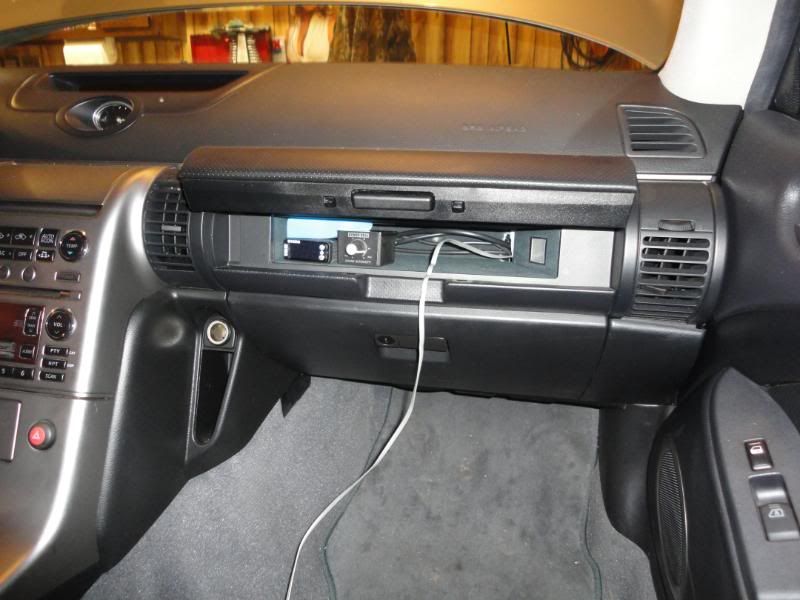
I could probably draw up a little wiring diagram showing how the factory wiring is done, and how mine is now if anyone would like it.
If you recall, I rewired the car last summer when I suspected weak spark causing a high RPM misfire at 16psi. Link, see post 48. That seemed to take care of the issue at the time. Now, with larger turbochargers and higher boost, the issue seems to have come back. I had tried different plugs and closing the spark plug gap up with only slight improvements.
The Boost-A-Spark is basically a voltage amplifier that takes whatever input voltage is, and increases it to whatever it is set to from 13.5V to 20V, adjustable via a control ****. This will push more voltage to the coils and in turn fire the plugs with more voltage. The unit can be active all the time by permanently connecting the trigger wires, or it can be activated at 4psi of boost using the supplied hobbs switch. I chose to use the switch and not run the higher voltage to the coils all the time.
You'll see in the link I mention that the wiring was sorted out. I had run a power feed for each coil and each IVTC solenoid to a junction behind the battery in case I needed to seperate the circuits at a later time. I decided this was the best way to accomplish this as if you just wire the BAS in series as the instructions depict, it would also be sending the higher voltage to the IVTC solenoids, I was not comfortable with that.
So I went back and seperated the 2 IVTC solenoid power wires, the 6 coil power wires, and the feed.
Now the next issue. This unit has a 10ga. power feed wire and a 30 amp fuse, to create a higher voltage, this thing needs some current flow. Once again if connected as the instructions depict, it would be connected to a tiny 14ga. (which might even be 16ga.) wire that has a 15 amp fuse protecting it. I decided to use the factory ignition wire that is also powering the IVTC solenoids to close a relay and connect the positive lead of the Boost-A-Spark directly to the battery through its fuse, of course.
All said and done it seems to work. Using my Fluke meter I set the output to 16V and went for a test drive.
It's in the 30's outside, so traction was non-existant and I can't tell if it's breaking up anymore or not as I can't load the thing down. Maybe tomorrow I can get a better test.
Here are a few pictures.
Here is the unit and what it comes with, the control ****, hobbs switch, wiring, and a few other odds and ends.
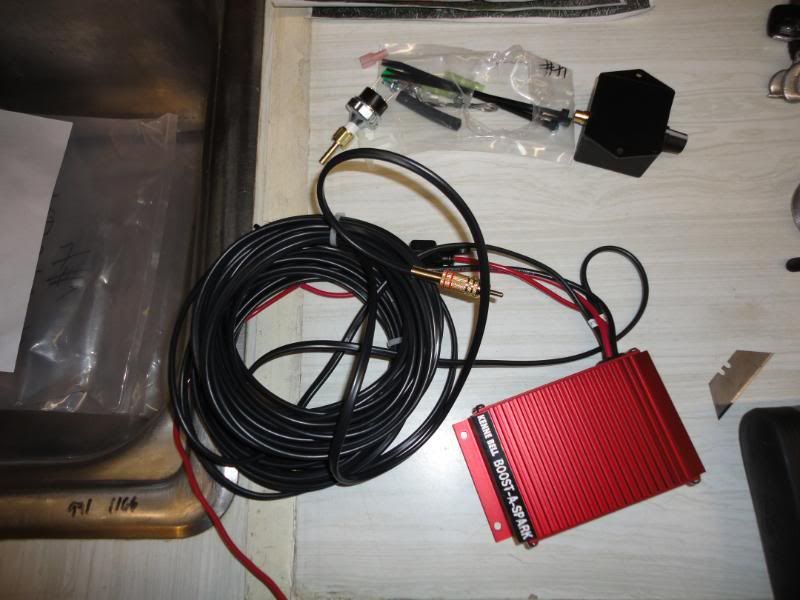
Under the hood before the install.
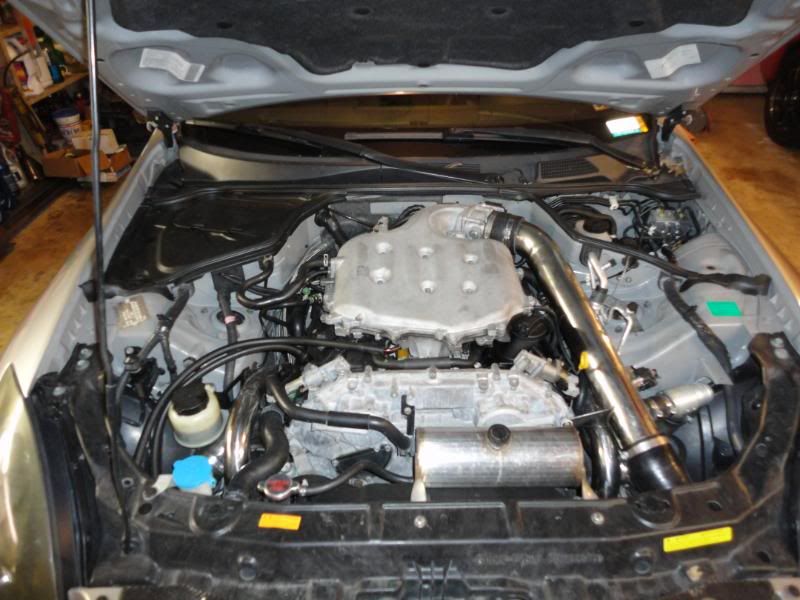
Removing the battery and such.
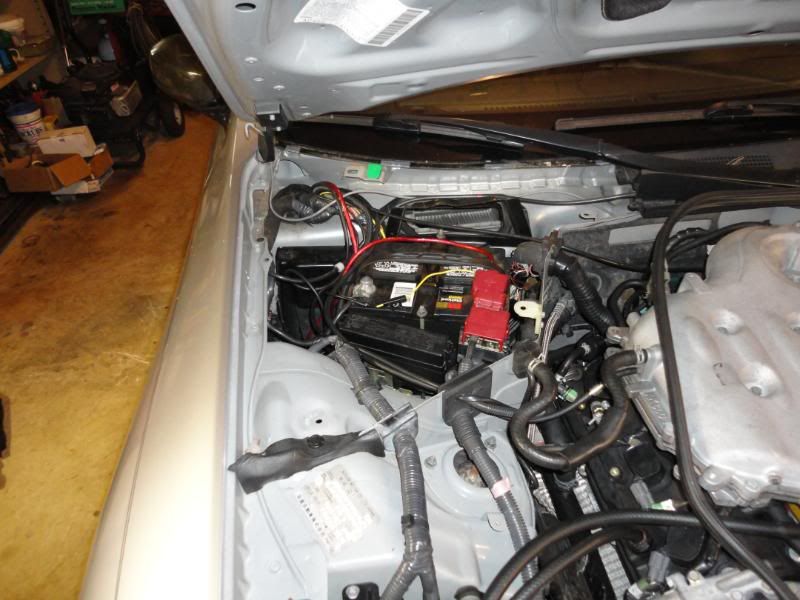
Seperating the coil and IVTC circuits.
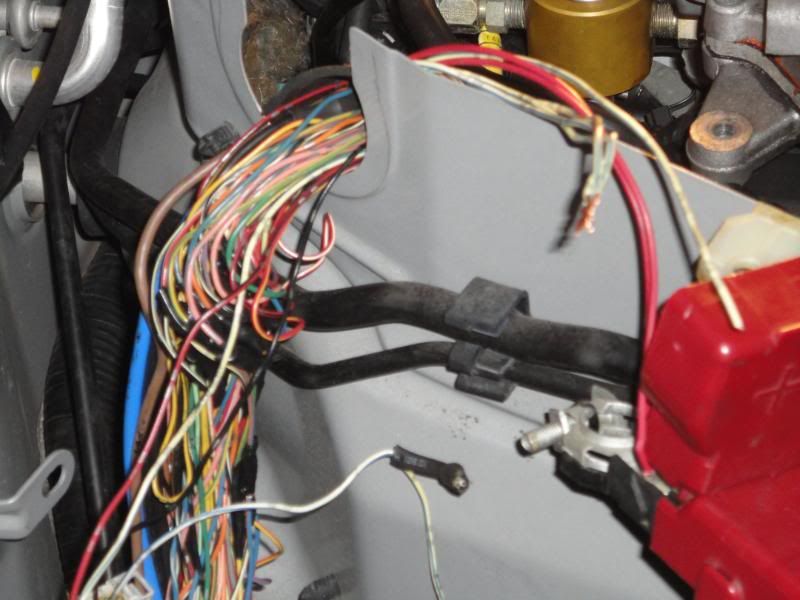
Adding the relay circuit to the BAS.
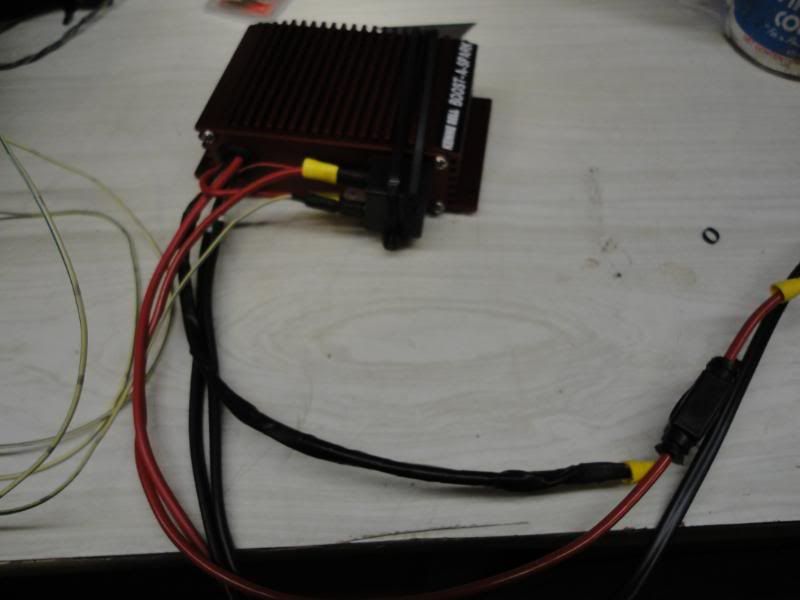
Location of the BAS.
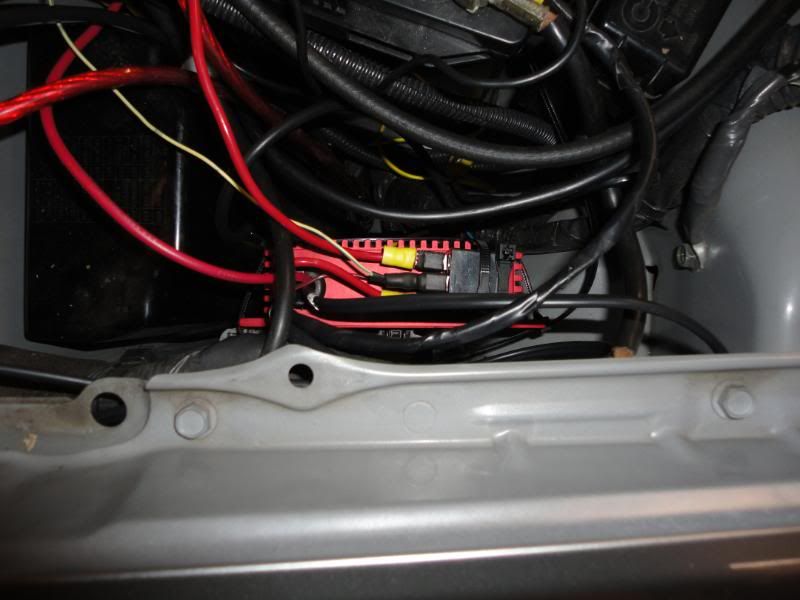
The red car got jealous, it's such an attention *****.
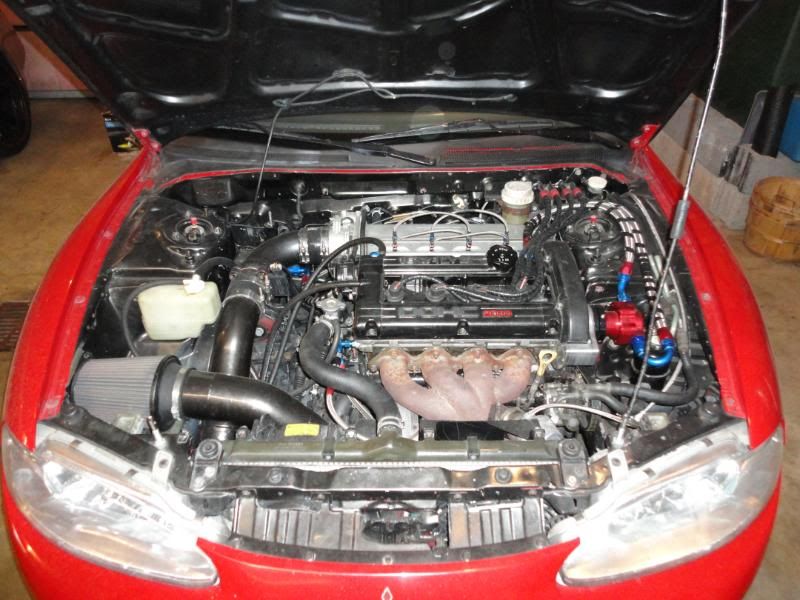
Buttoning it up.
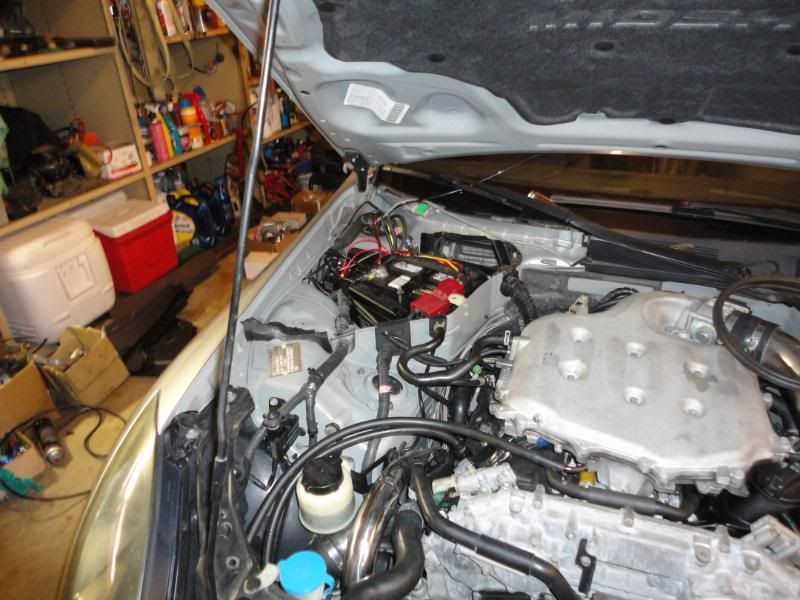
Finished.

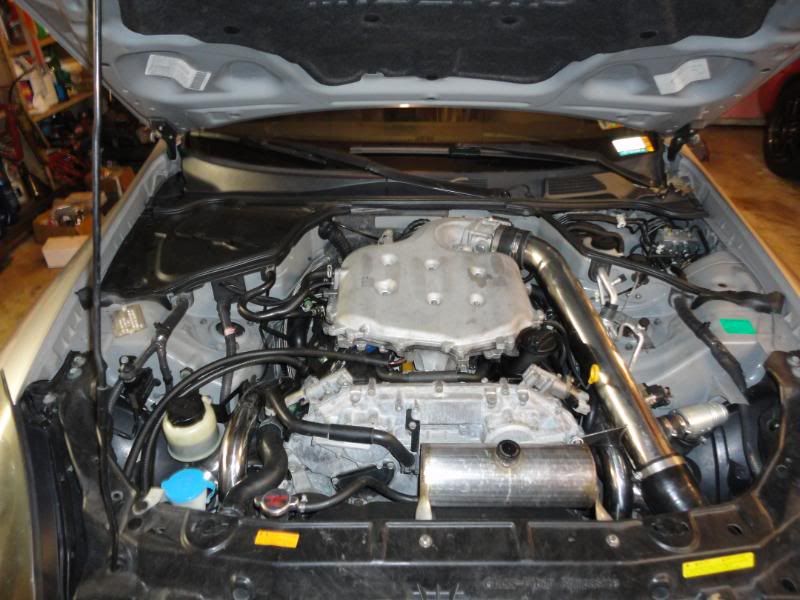
The adjustment ****.
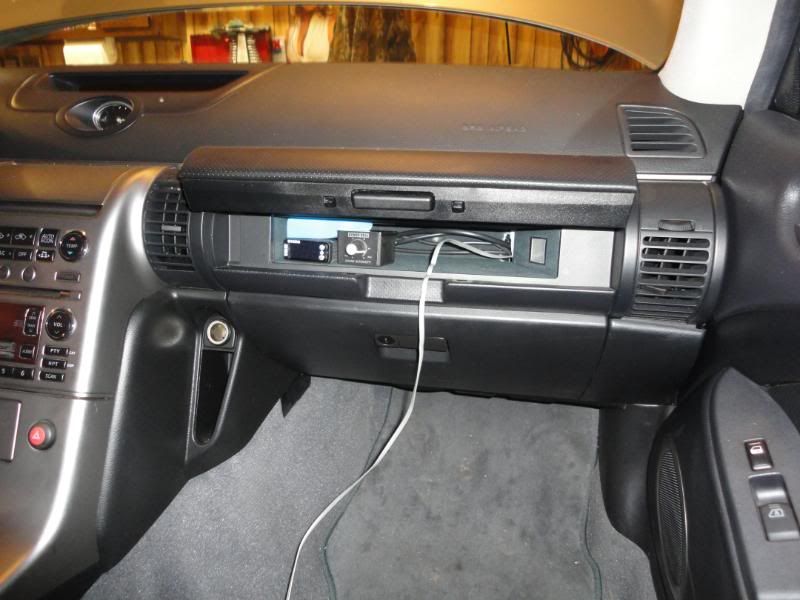
I could probably draw up a little wiring diagram showing how the factory wiring is done, and how mine is now if anyone would like it.
Last edited by BlinkerFluid; 12-03-2010 at 07:30 PM.
#68
New Member
Thread Starter
iTrader: (7)
Join Date: Apr 2007
Location: York County, Pennsylvania.
Posts: 211
Likes: 0
Received 0 Likes
on
0 Posts

I decided to stop using Osiris and move on to something a little better suited for my build.
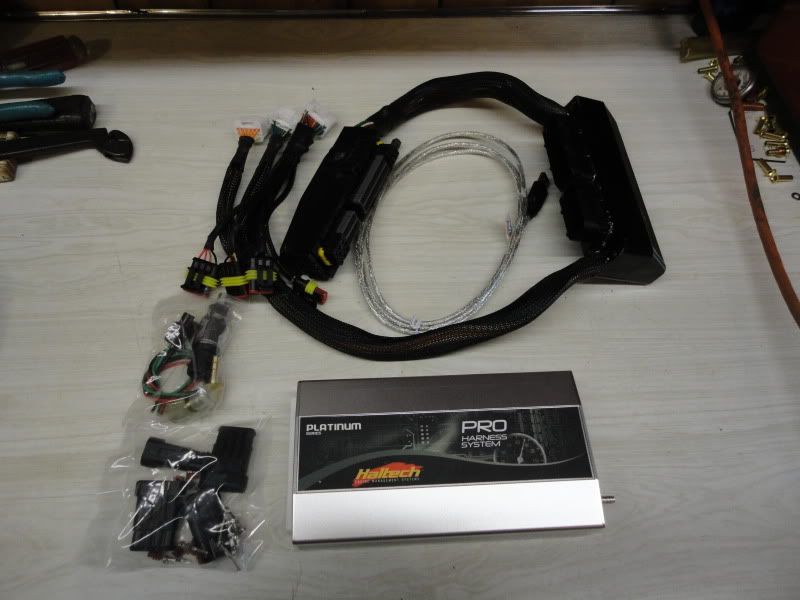
Haltech Pro Harness. This thing is sweet. I initially expected this worked like a UTEC, and at a set point, took over running the coils and injectors from the ECU. In reality, this thing is a stand alone.
I wired in a few relays, one will allow me no lift to shift/2-step and another to allow brake boosting. I also added a Kavilco 3.5 Bar MAP sensor because the internal sensor in the Haltech only reads to 22psi, and I hope to pass that point in the future.
The Haltech really amazes me, it has it's own short and long term fuel trims, and offers full control of every aspect of engine operation. I wish I had started with this piece long ago.
I also ordered a second wideband controller and sensor, a Zietronix ZT-3, so I can do bank by bank fuel trims. The ID2000 fuel injectors and a few hose ends should be coming in on Tuesday to finish the fuel system and get the car ready for E85.
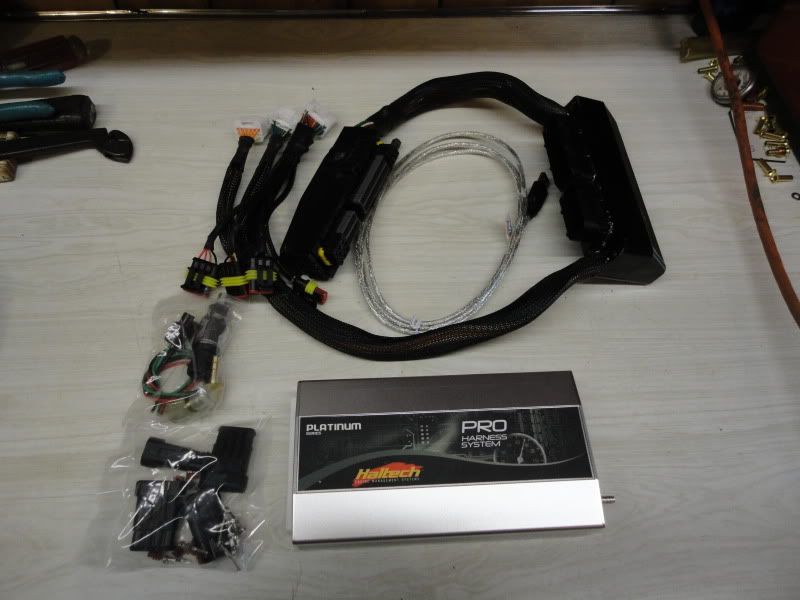
Haltech Pro Harness. This thing is sweet. I initially expected this worked like a UTEC, and at a set point, took over running the coils and injectors from the ECU. In reality, this thing is a stand alone.
I wired in a few relays, one will allow me no lift to shift/2-step and another to allow brake boosting. I also added a Kavilco 3.5 Bar MAP sensor because the internal sensor in the Haltech only reads to 22psi, and I hope to pass that point in the future.
The Haltech really amazes me, it has it's own short and long term fuel trims, and offers full control of every aspect of engine operation. I wish I had started with this piece long ago.
I also ordered a second wideband controller and sensor, a Zietronix ZT-3, so I can do bank by bank fuel trims. The ID2000 fuel injectors and a few hose ends should be coming in on Tuesday to finish the fuel system and get the car ready for E85.
#69
New Member
Thread Starter
iTrader: (7)
Join Date: Apr 2007
Location: York County, Pennsylvania.
Posts: 211
Likes: 0
Received 0 Likes
on
0 Posts

Recieved my second wideband and the fittings tonight. I got the wideband installed so now I can use wideband correction by bank.
Pre-install pic.
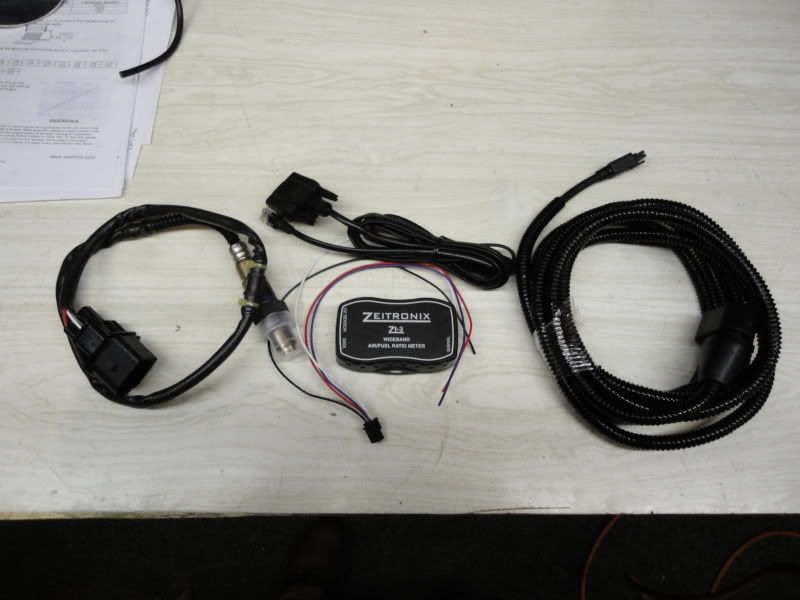
I would post a post-install pic, but there is no display, it only sends data to the Haltech.
Pre-install pic.
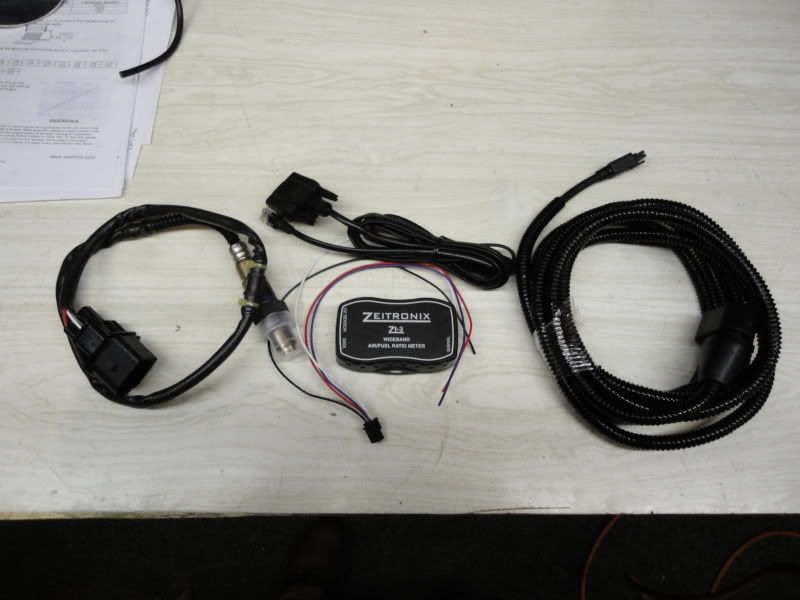
I would post a post-install pic, but there is no display, it only sends data to the Haltech.
#70
New Member
Thread Starter
iTrader: (7)
Join Date: Apr 2007
Location: York County, Pennsylvania.
Posts: 211
Likes: 0
Received 0 Likes
on
0 Posts

I've spent the past 2 days sorting out the fuel system. The APS Extreme Fuel System is a pair of Walbro GSS342 pumps (255HP) intank, dual -6 feed lines, dual Bosch 4 bar fuel pressure regulators and the factory feed line as a return.
In preperation for the 2000cc/min injectors, I need to be able to turn the fuel pressure down from the 58psi base to be able to get these things to idle on gasoline.
I started by removing the Bosch regulators and installing the old Aeromotive adjustable fuel pressure regulator from the red car. Once I fit up a few lines, made a mounting bracket and got the car running, I realized I had a larger problem that I didn't know existed.
Fuel pressure overrun. No matter what I tried I couldn't get fuel pressure to decrease below 65psi. I busted out a few extra lines and fittings I had laying around and started testing for backpressure in the fuel return line. Sure enough, 65psi of backpressure. Now to determine the cause. With the pumps running (they both run all the time) I tested at the beginning of the return line, and at the end of the return line.
The line itself showed about 40psi of backpressure, but when I installed the gauge at the return fitting going into the fuel basket, I found the issue. There is a siphon jet pump that uses return fuel flow and a venturi to pull fuel from the sump of the driver's side of the tank to the passenger's side, where the fuel pumps reside. This piece exists in the factory setup, but the APS fuel hanger completely replaces the unit, and the siphon pump was built by APS.
Up until this point I was very impressed with the engineering and build quality behind the APS products, but designing a fuel system that can't handle the return fuel from the pumps they supply is unacceptable. I never checked fuel pressure on the APS fuel system, but I know it could not have been any lower than 65psi, and with the regulators base fuel pressure of 58psi, fuel pressure was not correct unitl the intake manifold was seeing 7psi of boost.
Though not a huge deal, it would have made tuning the 2000cc injectors difficult to dial in at low load on gasoline.
I disassembled the fuel pump hanger and took a hard look at the siphon pump. Through a bit of testing with some vacuum gauges and air pressure, I came up with a new orifice size and tube size that would allow more fuel to return to the tank and continue to pull fuel from the driver's side of the tank.
The idea of the siphon pump, jet pump, venturi pump, whatever you want to call it is velocity and change of area. A fluid enters through an orifice at a high velocity into a tube or chamber of larger diameter, where it slows, causing a decrease in dynamic pressure. A port is placed right at this diameter change and the vacuum is tapped to pull fuel.
Ending up with a .200" venturi diameter and .310" tube diameter and installing it in the tank for real world testing, I had successfully modded the pump. Now it continues to pull fuel from the driver's side of the tank, and I can turn the fuel pressure down to the next highest restriction, the line at 40psi. If this isn't sufficient, I'll have to disable one of the pumps at low power levels. Though I think I should be alright how it is.
Here are a few pictures of the process.
APS regulator.
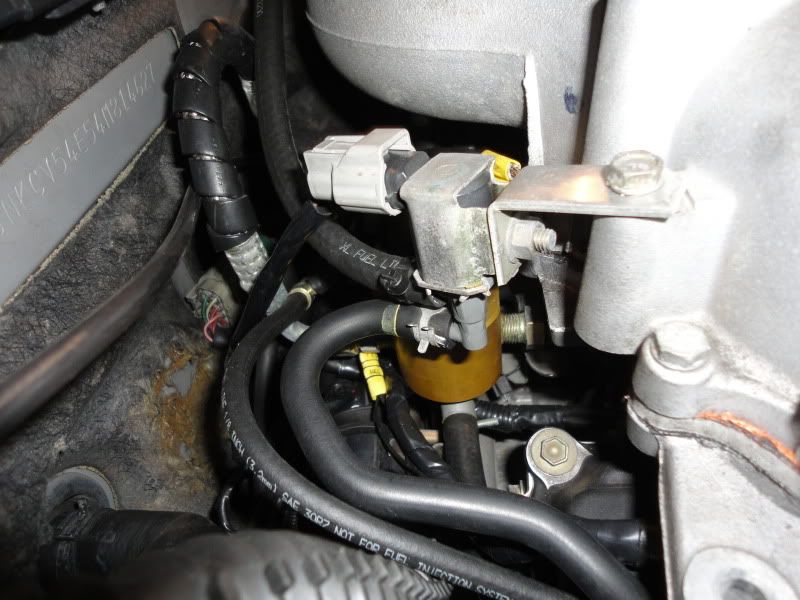
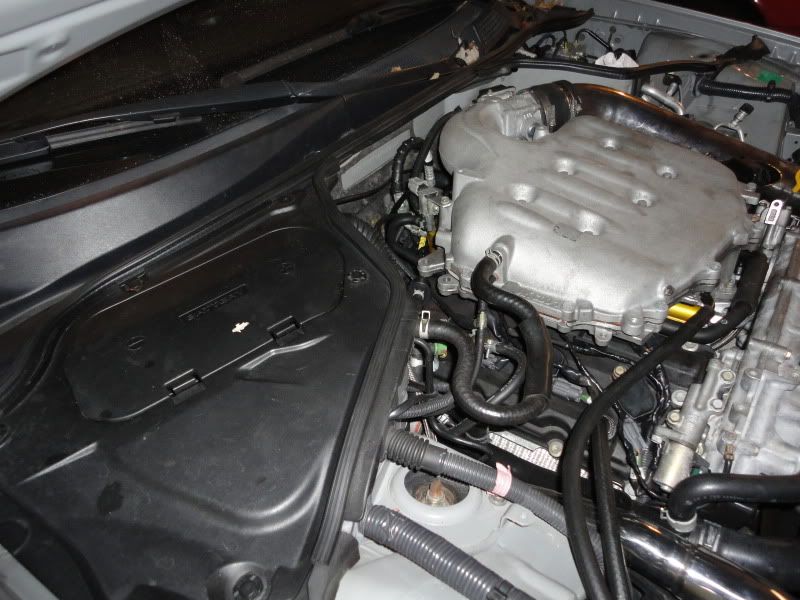
APS rails and regulators.
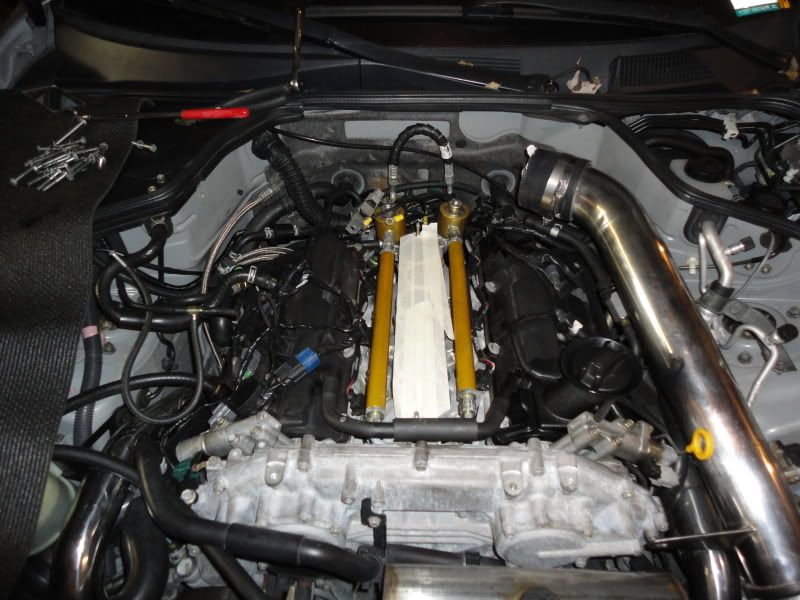
Aeromotive regulator and lines.
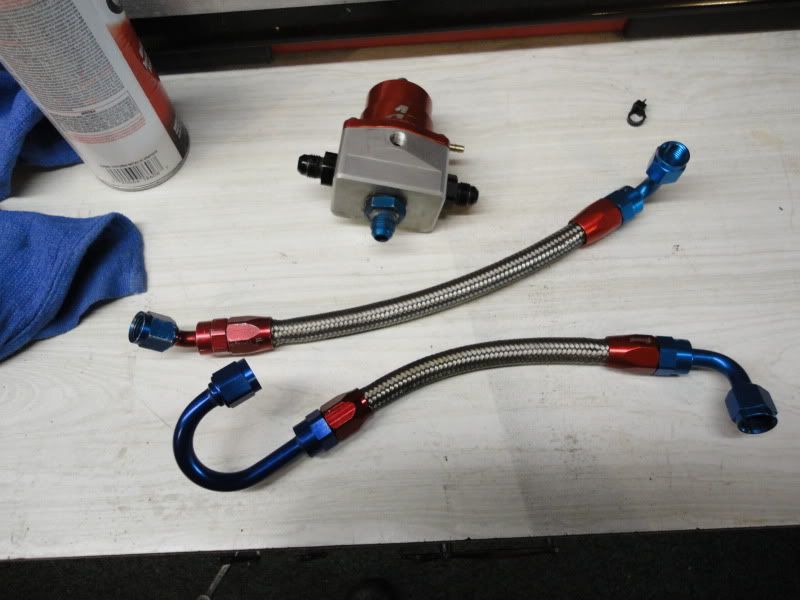
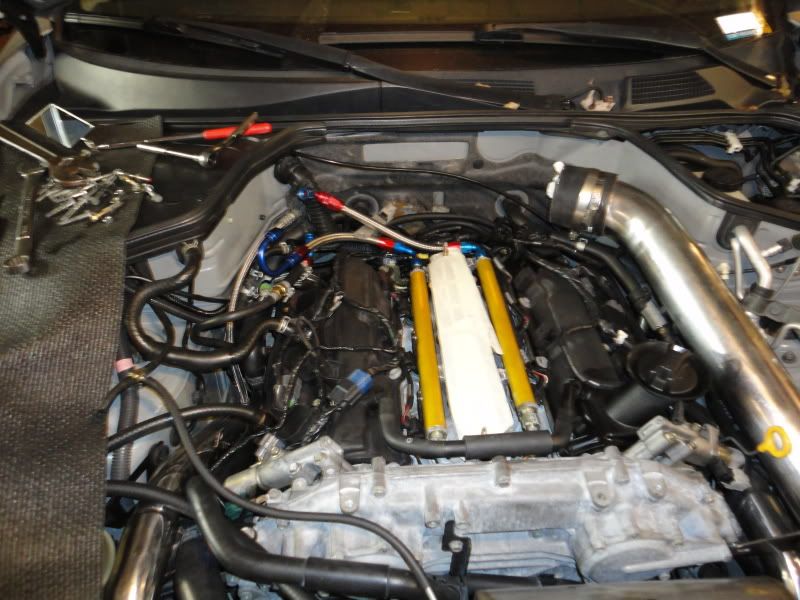
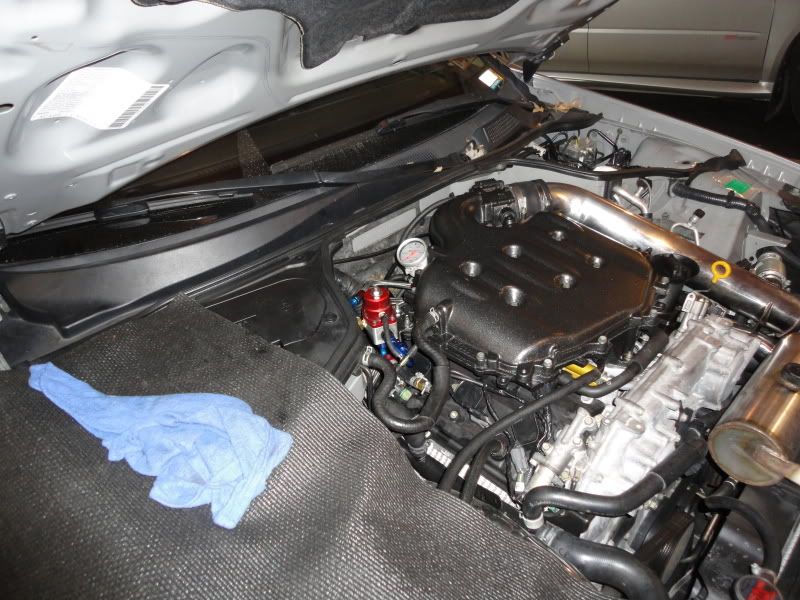
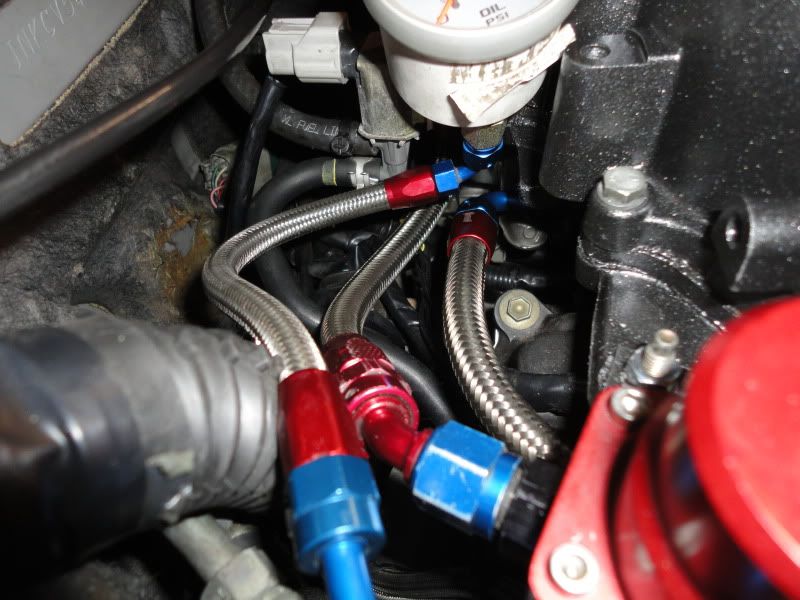
I also added some color to the intake manifold/plenum.
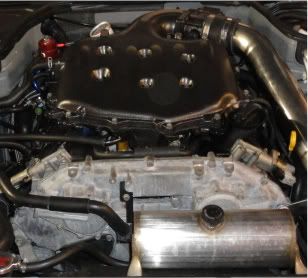
The fuel (oil) pressure gauge is temporary for setup. My other compact fuel gauge is broken so it was all I had.
Unfortunately, I didn't get any pictures of the whole siphon pump process since I was covered in gasoline and didn't want to get it all over my camera.
In preperation for the 2000cc/min injectors, I need to be able to turn the fuel pressure down from the 58psi base to be able to get these things to idle on gasoline.
I started by removing the Bosch regulators and installing the old Aeromotive adjustable fuel pressure regulator from the red car. Once I fit up a few lines, made a mounting bracket and got the car running, I realized I had a larger problem that I didn't know existed.
Fuel pressure overrun. No matter what I tried I couldn't get fuel pressure to decrease below 65psi. I busted out a few extra lines and fittings I had laying around and started testing for backpressure in the fuel return line. Sure enough, 65psi of backpressure. Now to determine the cause. With the pumps running (they both run all the time) I tested at the beginning of the return line, and at the end of the return line.
The line itself showed about 40psi of backpressure, but when I installed the gauge at the return fitting going into the fuel basket, I found the issue. There is a siphon jet pump that uses return fuel flow and a venturi to pull fuel from the sump of the driver's side of the tank to the passenger's side, where the fuel pumps reside. This piece exists in the factory setup, but the APS fuel hanger completely replaces the unit, and the siphon pump was built by APS.
Up until this point I was very impressed with the engineering and build quality behind the APS products, but designing a fuel system that can't handle the return fuel from the pumps they supply is unacceptable. I never checked fuel pressure on the APS fuel system, but I know it could not have been any lower than 65psi, and with the regulators base fuel pressure of 58psi, fuel pressure was not correct unitl the intake manifold was seeing 7psi of boost.
Though not a huge deal, it would have made tuning the 2000cc injectors difficult to dial in at low load on gasoline.
I disassembled the fuel pump hanger and took a hard look at the siphon pump. Through a bit of testing with some vacuum gauges and air pressure, I came up with a new orifice size and tube size that would allow more fuel to return to the tank and continue to pull fuel from the driver's side of the tank.
The idea of the siphon pump, jet pump, venturi pump, whatever you want to call it is velocity and change of area. A fluid enters through an orifice at a high velocity into a tube or chamber of larger diameter, where it slows, causing a decrease in dynamic pressure. A port is placed right at this diameter change and the vacuum is tapped to pull fuel.
Ending up with a .200" venturi diameter and .310" tube diameter and installing it in the tank for real world testing, I had successfully modded the pump. Now it continues to pull fuel from the driver's side of the tank, and I can turn the fuel pressure down to the next highest restriction, the line at 40psi. If this isn't sufficient, I'll have to disable one of the pumps at low power levels. Though I think I should be alright how it is.
Here are a few pictures of the process.
APS regulator.
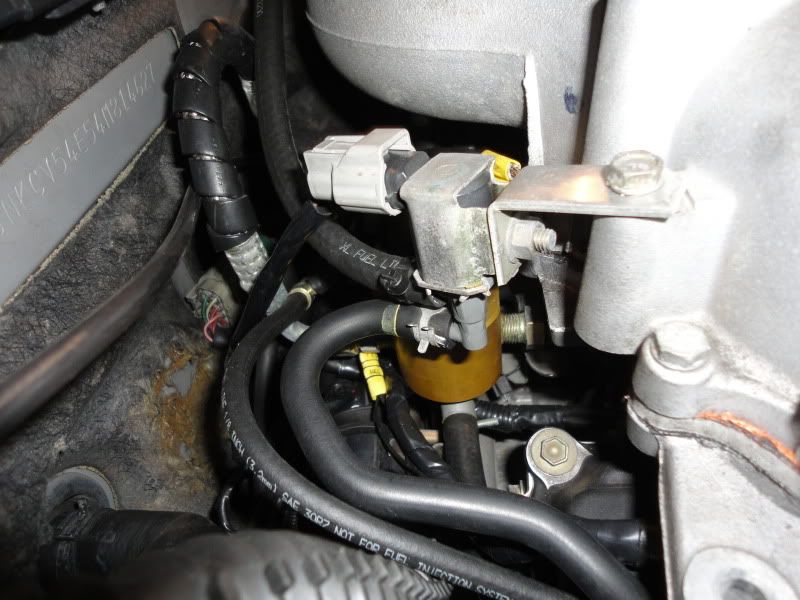
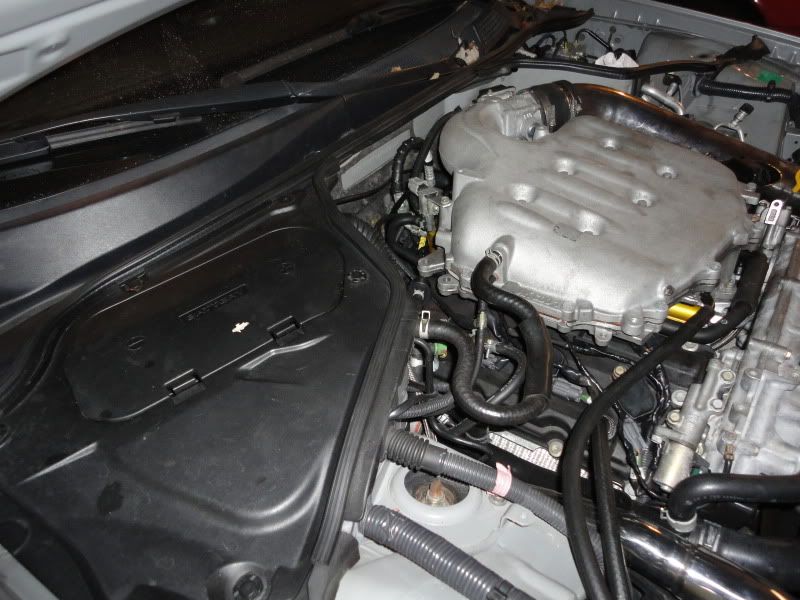
APS rails and regulators.
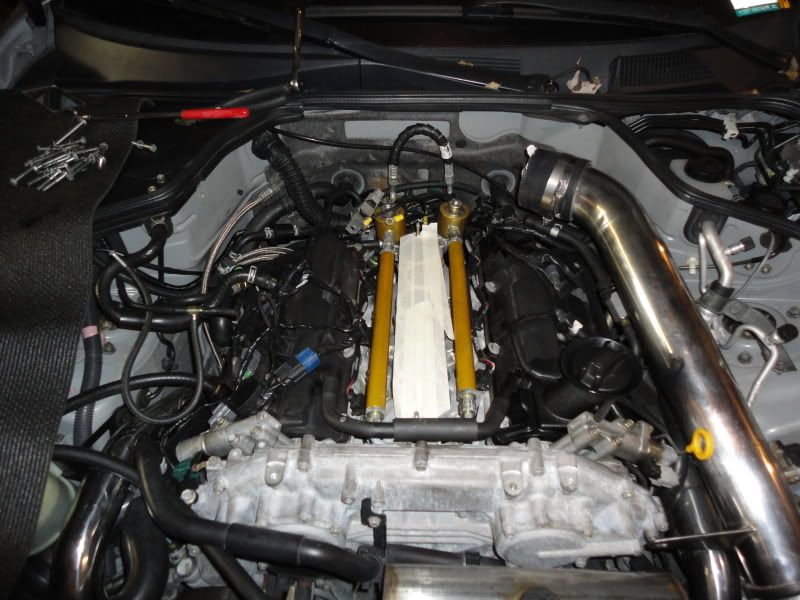
Aeromotive regulator and lines.
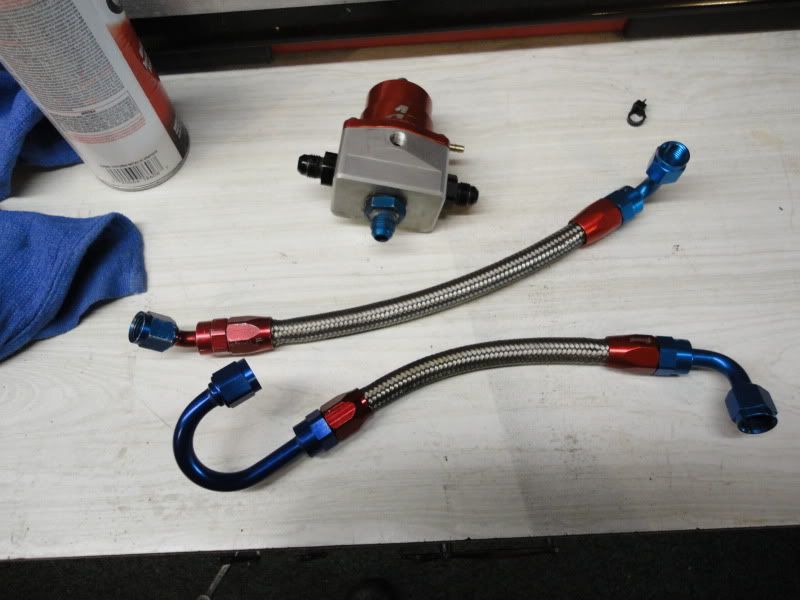
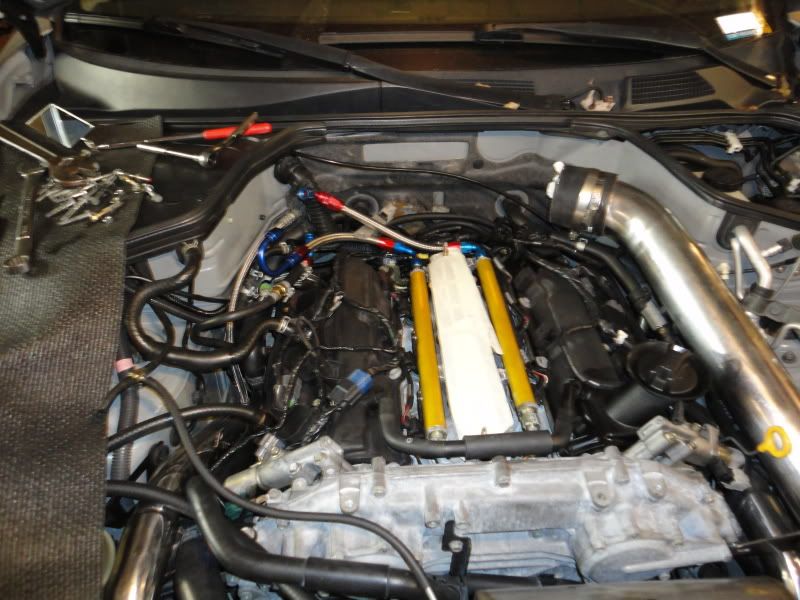
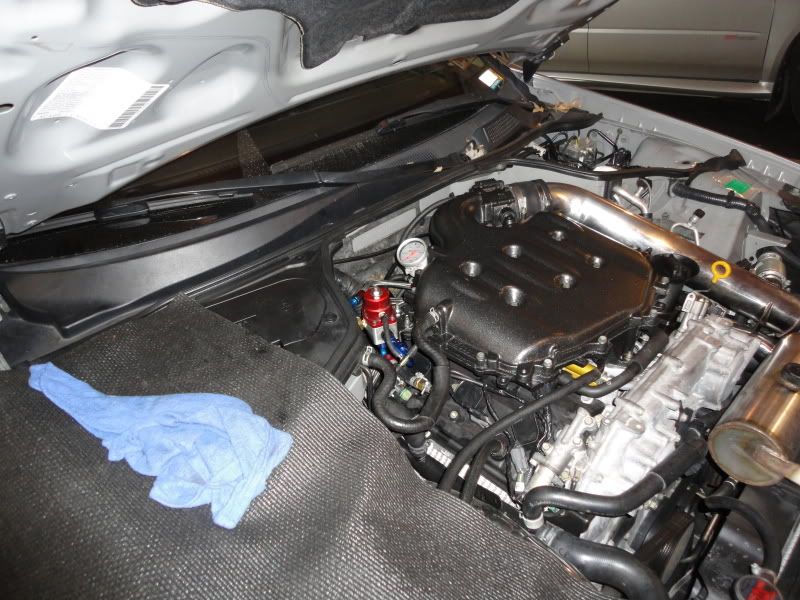
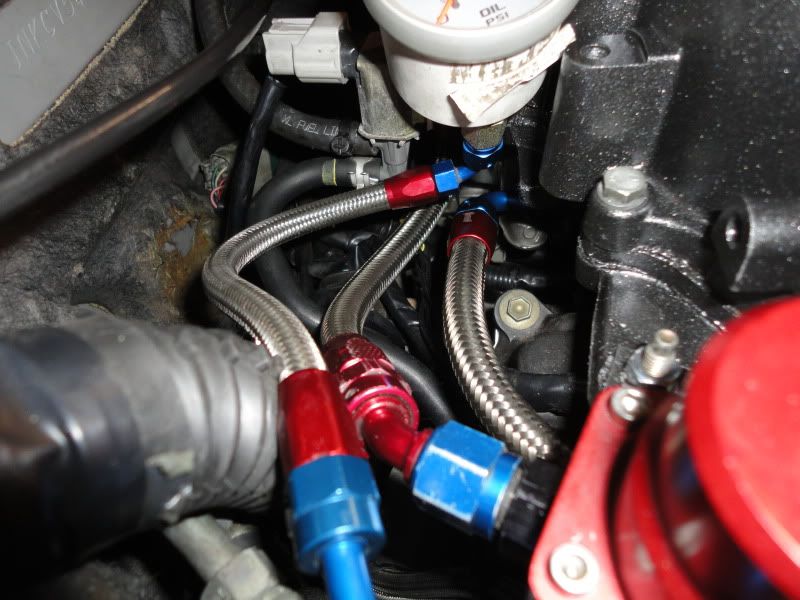
I also added some color to the intake manifold/plenum.
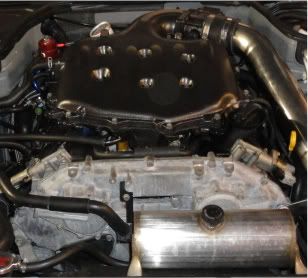
The fuel (oil) pressure gauge is temporary for setup. My other compact fuel gauge is broken so it was all I had.
Unfortunately, I didn't get any pictures of the whole siphon pump process since I was covered in gasoline and didn't want to get it all over my camera.
Last edited by BlinkerFluid; 03-26-2012 at 04:27 PM.
#71
New Member
iTrader: (11)

good luck. i have ID2000s as well. Based on my previous IPW with my 1200s, i'm gonna have to run into the low 30psi for base fuel pressure most likely. I'm already running a Hobbs switch on the second pump. You'll be dialed in way before me so interesting to see how it goes.
Why didnt you go with the ProEFI 128 box and have true flex fuel capability?
Why didnt you go with the ProEFI 128 box and have true flex fuel capability?
Last edited by str8dum1; 01-06-2011 at 06:49 AM.
#72
Registered User
iTrader: (2)
Join Date: Jul 2008
Location: Alabama
Posts: 497
Likes: 0
Received 0 Likes
on
0 Posts

Thanks for the info on the fuel system
are you not running a check valve in the PCV line off the plenum? i noticed oil on the fillerneck, mine did the same thing and actually screwed my oil cap off before i put in a check valve
are you not running a check valve in the PCV line off the plenum? i noticed oil on the fillerneck, mine did the same thing and actually screwed my oil cap off before i put in a check valve
#73
New Member
Thread Starter
iTrader: (7)
Join Date: Apr 2007
Location: York County, Pennsylvania.
Posts: 211
Likes: 0
Received 0 Likes
on
0 Posts

good luck. i have ID2000s as well. Based on my previous IPW with my 1200s, i'm gonna have to run into the low 30psi for base fuel pressure most likely. I'm already running a Hobbs switch on the second pump. You'll be dialed in way before me so interesting to see how it goes.
Why didnt you go with the ProEFI 128 box and have true flex fuel capability?
Why didnt you go with the ProEFI 128 box and have true flex fuel capability?
There is a check, it's just out of sight over behind the headlight.
#74
New Member
iTrader: (11)

Hal also sells ProEfi128... wonder why he doesnt push it more considering its such a superior EMS compared to Haltech at the current time.
Thats pretty crazy considering Walbros take a crap past 75psi of fuel pressure. If you were running 65psi base plus 20 psi, your pumps were putting out like 180LPH, so probably less than 350LPH (since you cant just double the rating for 2) That barely supports 900cc injectors at full tilt.
The APS Extreme Fuel System is a pair of Walbro GSS342 pumps (255HP) intank, dual -6 feed lines, dual Bosch 4 bar fuel pressure regulators and the factory feed line as a return.
Fuel pressure overrun. No matter what I tried I couldn't get fuel pressure to decrease below 65psi. I busted out a few extra lines and fittings I had laying around and started testing for backpressure in the fuel return line. Sure enough, 65psi of backpressure.
I never checked fuel pressure on the APS fuel system, but I know it could not have been any lower than 65psi, and with the regulators base fuel pressure of 58psi, fuel pressure was not correct unitl the intake manifold was seeing 7psi of boost.
Fuel pressure overrun. No matter what I tried I couldn't get fuel pressure to decrease below 65psi. I busted out a few extra lines and fittings I had laying around and started testing for backpressure in the fuel return line. Sure enough, 65psi of backpressure.
I never checked fuel pressure on the APS fuel system, but I know it could not have been any lower than 65psi, and with the regulators base fuel pressure of 58psi, fuel pressure was not correct unitl the intake manifold was seeing 7psi of boost.
Last edited by str8dum1; 01-07-2011 at 09:29 AM.
#75
New Member
Thread Starter
iTrader: (7)
Join Date: Apr 2007
Location: York County, Pennsylvania.
Posts: 211
Likes: 0
Received 0 Likes
on
0 Posts

Hal also sells ProEfi128... wonder why he doesnt push it more considering its such a superior EMS compared to Haltech at the current time.
Thats pretty crazy considering Walbros take a crap past 75psi of fuel pressure. If you were running 65psi base plus 20 psi, your pumps were putting out like 180LPH, so probably less than 350LPH (since you cant just double the rating for 2) That barely supports 900cc injectors at full tilt.
Thats pretty crazy considering Walbros take a crap past 75psi of fuel pressure. If you were running 65psi base plus 20 psi, your pumps were putting out like 180LPH, so probably less than 350LPH (since you cant just double the rating for 2) That barely supports 900cc injectors at full tilt.
Just to be clear, the base wasn't 65psi, it was still 58 as per the regulator. The restriction on the return was holding the pressure at 65. That pressure was not rising until the regulator was requesting a pressure higher than 65psi. Once the regulator dome saw 8psi of pressure, it would raise fuel pressure 1psi to 66psi. Below 8 psi of boost, fuel pressure was always 65psi, though the system only required 65psi when the engine was seeing 7psi of boost. I can't really call it base fuel pressure when it is not the intended differential pressure across the injectors.
Actually, I'll do a test at pressure on the pumps. Since I have the adjustable regulator on the car now I'll see if I can get some semi-accurate flow numbers at different pressures. That wouldn't be bad real world numbers to have floating around. I can start at the lowest I can set it now (~40psi) and go up in 10psi increments. I can also try a couple of voltage levels.
I've done similar tests with Walbro pumps and my DSM back in the day, but it was a single -6 feed to the rail.
Also, you can give the Walbros a good shot in the arm at higher pressures by disabling the pressure relief valve. Not recommended by the manufacturer of course, but it's very very common in the DSM/EVO world to get the flow necissary at the higher pressures needed for smaller displacement to make big power.
Damn, that was a mouthfull!

I do wish I had looked into the ProEFI a bit more. I've already been through the Uni-chip, UTEC, and Osiris. Now with the Haltech on the car who knows what the future holds.
#76
New Member
Thread Starter
iTrader: (7)
Join Date: Apr 2007
Location: York County, Pennsylvania.
Posts: 211
Likes: 0
Received 0 Likes
on
0 Posts

Here we go!
I picked up the ID2000 injectors on Saturday afternoon. It took a bit of modification to get them to fit the car. I removed the APS fuel injectors, which are Siemens FI114962 or 107-962 650cc/min. APS jacks up the base fuel pressure to get more flow out of them.
They are a short injector with 14mm top and bottom o-rings. I got the shortest (grey) 14mm o-ring adapters for the ID2000 injectors, this makes them about .300" longer than the Siemens injectors. Overall, the ID2000 and the Siemens are the same length, but the ID2000 will sit farther into the lower intake runners than the Siemens. The adaptors contain 7 micron filters, as the ID2000s do not have inlet filters. I could have shortened the fuel rail mounts and used the IDs without the adapters and filters, or make new rail mounts and use the adaptors.
After weighing it over and looking at what modification was necissary, I decided to make longer rail brackets and use the adaptors. The issue was the rails would hit the bottom of the lower plenum. After a bit of tiral and error, I saw that I would have to remove some material from the flange of the lower plenum. I was going to take the part down to my buddies machine shop, fit it in the mill and cut it. Looking around my garage I noticed an old handheld belt sander, and the radius of the front guide wheel would cut the perfect curve in the lower plenum. Half an hour later I had the cutting done and fabricated new fuel rail mounting brackets.
One nice thing was the ID2000s use the exact same connector as the stock 350Z/G35 injectors, so I didn't have to do any wiring for this project. Plug in the stock injector harness and go.
I installed the lower runners, injectors, and rails on the car, hooked up all the fuel lines and ran the fuel pumps to check for leaks. With none to be found I reassembled the car and did a bit of fuel system testing.
I have some data to go through, ugh.
After the testing was complete, I went into getting the car to start and idle. In a short amount of time I had her running and went for a short drive. I still have a bit of work to do on low load and idle, but WOT was close at 12psi, and injector duty cycle barely hit 30%.
It seems at a 40psi base, I'm not going to be able to get a perfect 14.7 AFR idle on gasoline, but I still have some fine tuning to do. 13.7 may be attainable, and I may try to rework the return line to turn the pressure down to a 30psi base.
E85 will be a completely different story I should be able to get it to do whatever I want.
Here are some pictures.
New injectors and adaptors.
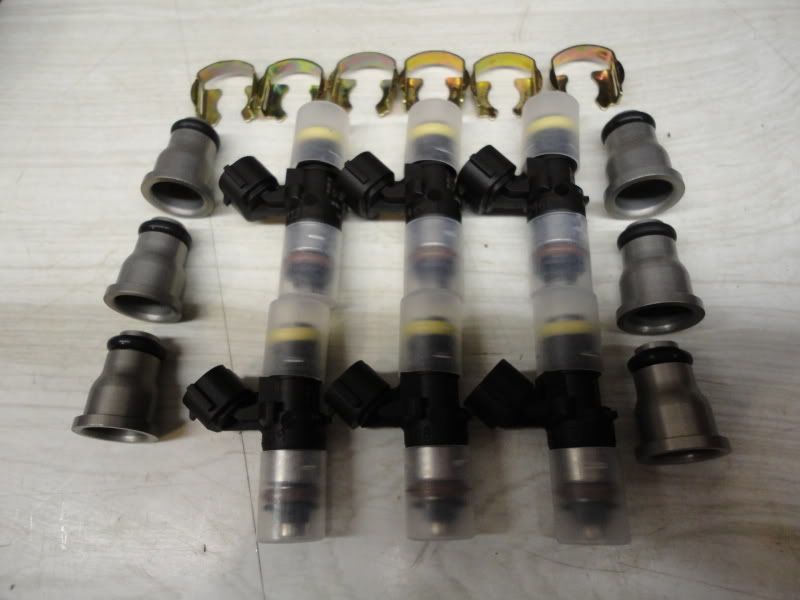
Stock lower plenum flange.
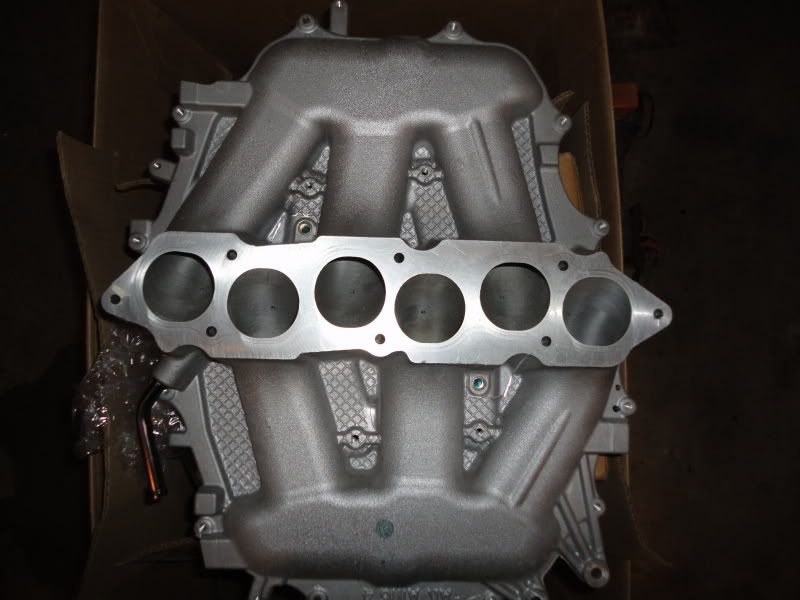
Modified lower plenum.
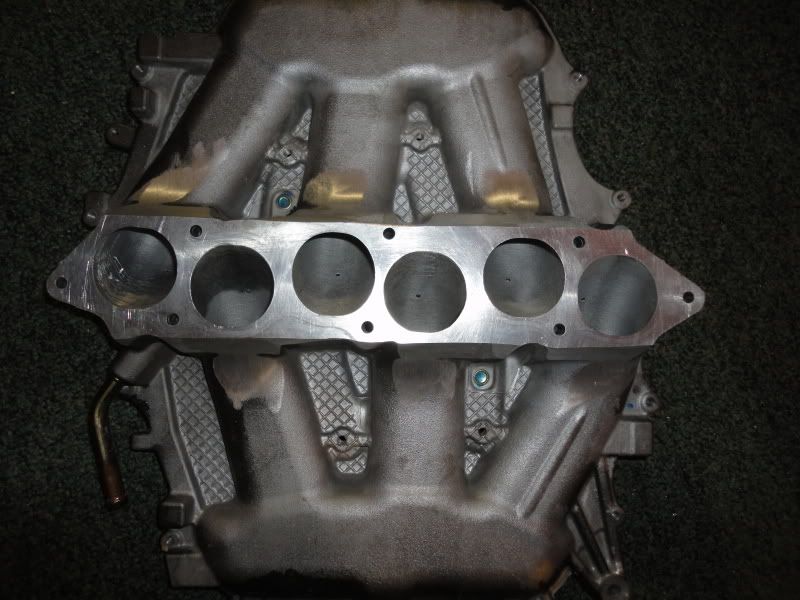

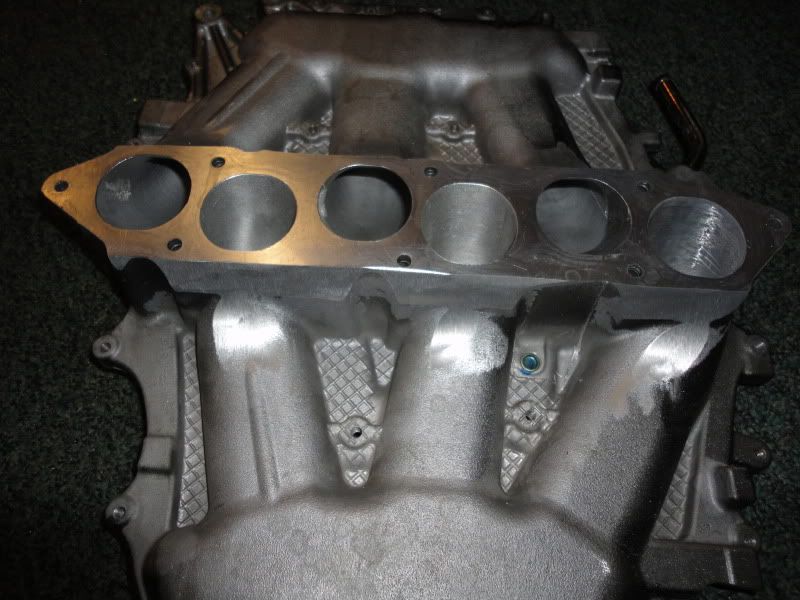
Injectors installed and new rail brackets.
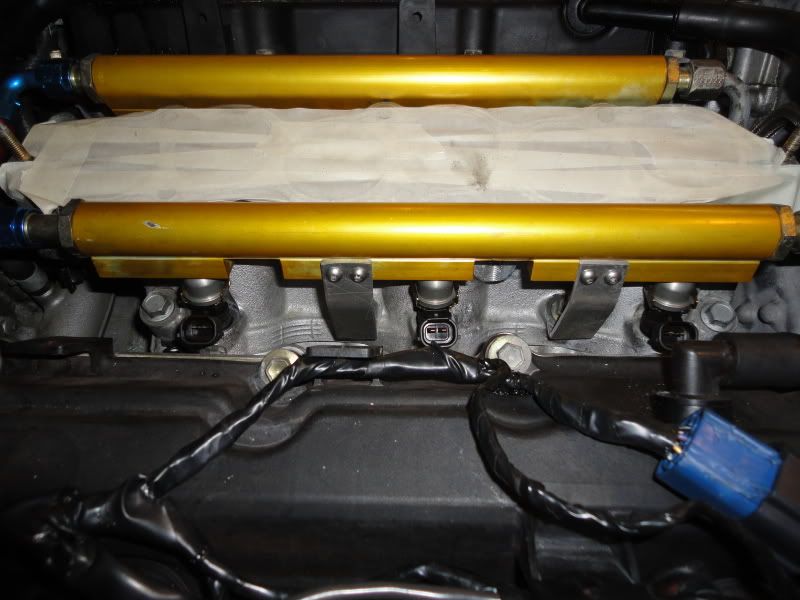
I'll spend some time getting the drivability and idle good, then toss it on the dyno for a pump gas tune. After that, I'll fill 'er up with corn juice and see what happens.
I picked up the ID2000 injectors on Saturday afternoon. It took a bit of modification to get them to fit the car. I removed the APS fuel injectors, which are Siemens FI114962 or 107-962 650cc/min. APS jacks up the base fuel pressure to get more flow out of them.
They are a short injector with 14mm top and bottom o-rings. I got the shortest (grey) 14mm o-ring adapters for the ID2000 injectors, this makes them about .300" longer than the Siemens injectors. Overall, the ID2000 and the Siemens are the same length, but the ID2000 will sit farther into the lower intake runners than the Siemens. The adaptors contain 7 micron filters, as the ID2000s do not have inlet filters. I could have shortened the fuel rail mounts and used the IDs without the adapters and filters, or make new rail mounts and use the adaptors.
After weighing it over and looking at what modification was necissary, I decided to make longer rail brackets and use the adaptors. The issue was the rails would hit the bottom of the lower plenum. After a bit of tiral and error, I saw that I would have to remove some material from the flange of the lower plenum. I was going to take the part down to my buddies machine shop, fit it in the mill and cut it. Looking around my garage I noticed an old handheld belt sander, and the radius of the front guide wheel would cut the perfect curve in the lower plenum. Half an hour later I had the cutting done and fabricated new fuel rail mounting brackets.
One nice thing was the ID2000s use the exact same connector as the stock 350Z/G35 injectors, so I didn't have to do any wiring for this project. Plug in the stock injector harness and go.
I installed the lower runners, injectors, and rails on the car, hooked up all the fuel lines and ran the fuel pumps to check for leaks. With none to be found I reassembled the car and did a bit of fuel system testing.
I have some data to go through, ugh.
After the testing was complete, I went into getting the car to start and idle. In a short amount of time I had her running and went for a short drive. I still have a bit of work to do on low load and idle, but WOT was close at 12psi, and injector duty cycle barely hit 30%.
It seems at a 40psi base, I'm not going to be able to get a perfect 14.7 AFR idle on gasoline, but I still have some fine tuning to do. 13.7 may be attainable, and I may try to rework the return line to turn the pressure down to a 30psi base.
E85 will be a completely different story I should be able to get it to do whatever I want.
Here are some pictures.
New injectors and adaptors.
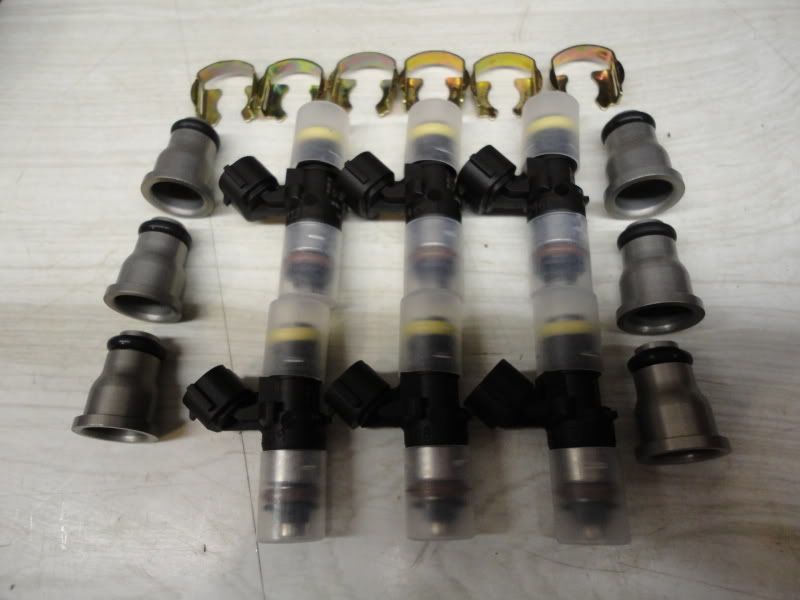
Stock lower plenum flange.
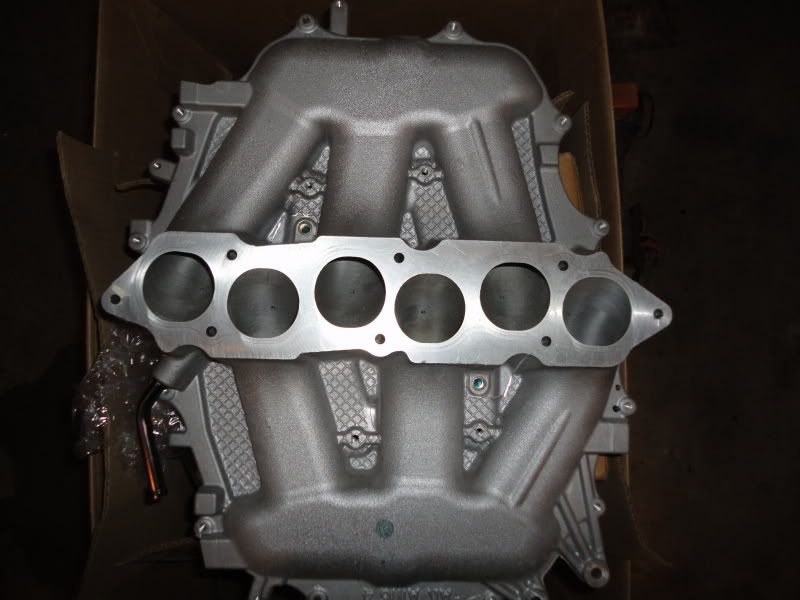
Modified lower plenum.
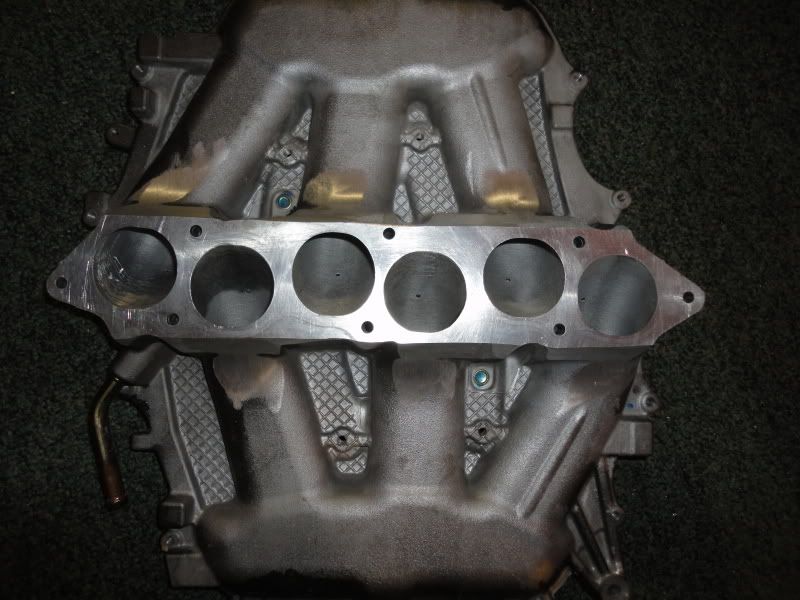

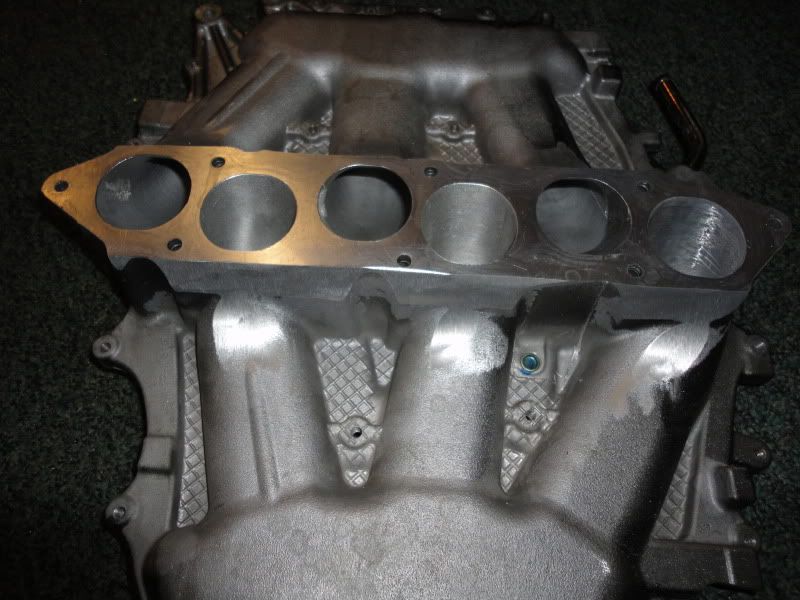
Injectors installed and new rail brackets.
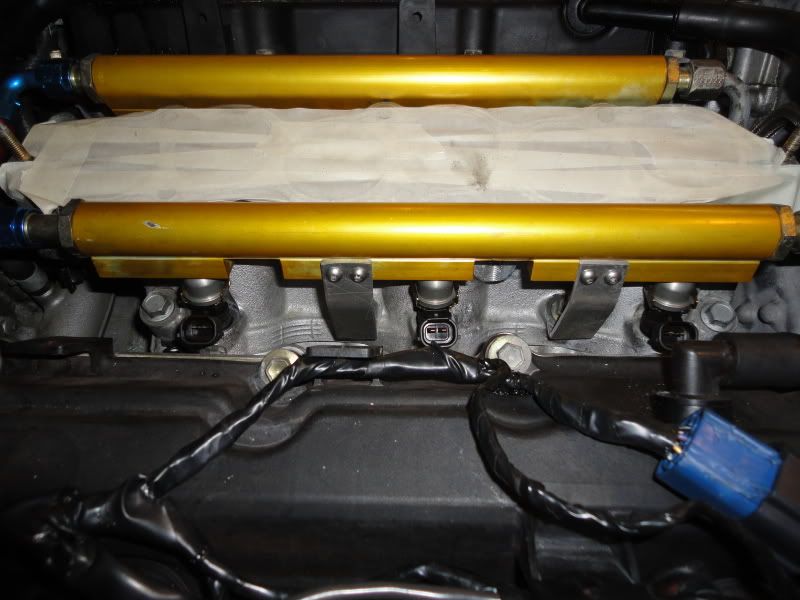
I'll spend some time getting the drivability and idle good, then toss it on the dyno for a pump gas tune. After that, I'll fill 'er up with corn juice and see what happens.
Last edited by BlinkerFluid; 03-26-2012 at 04:33 PM.
#79
New Member
Thread Starter
iTrader: (7)
Join Date: Apr 2007
Location: York County, Pennsylvania.
Posts: 211
Likes: 0
Received 0 Likes
on
0 Posts

I haven't had much time to work with it. Cold, warm, and hot start are good. Transient throttle is good. Idle still needs attention though it's not that bad, just a bit rich.
I did go for a short drive and even stood on the throttle. Light load needs cleaned up and she's way rich up top but it was cool to see <30% injector duty cycle at a boost level where the car made ~500WHP.
I expect to be able to get a solid 12.5-13.0AFR at idle with the current fuel pressure, which should be ok. I did a bit of research on bore wash and it does not seem to be a concern until the low 10AFRs or even more rich. Since these injectors are touted for their atomization, I'm confident I won't hurt the engine.
I did run a few fuel system tests at various pressures. Of note is at 13.8V, my Walbro 255HP's pushed 474LPH of fuel to the engine compartment at 70psi. Unfortunately, I didn't have a good way to keep voltage stable while turning the pressure up, so I feel some of the flow loss at higher pressures are a result of dropping voltage. I have the Walbro relief valves disabled. With the car running the pumps get a steady 14-14.1V. I was already using gasoline as a test fluid, I wasn't brave enough to do it with the engine running.
I have tests showing 40, 50, 60, and 70psi with the battery charger on the low setting, and 50, 60, 70, 80, and 90 with it on the high setting. As I mentioned, without a good regulating power supply, as pressure goes up, voltage goes down and flow does as well, as expected.
I did go for a short drive and even stood on the throttle. Light load needs cleaned up and she's way rich up top but it was cool to see <30% injector duty cycle at a boost level where the car made ~500WHP.
I expect to be able to get a solid 12.5-13.0AFR at idle with the current fuel pressure, which should be ok. I did a bit of research on bore wash and it does not seem to be a concern until the low 10AFRs or even more rich. Since these injectors are touted for their atomization, I'm confident I won't hurt the engine.
I did run a few fuel system tests at various pressures. Of note is at 13.8V, my Walbro 255HP's pushed 474LPH of fuel to the engine compartment at 70psi. Unfortunately, I didn't have a good way to keep voltage stable while turning the pressure up, so I feel some of the flow loss at higher pressures are a result of dropping voltage. I have the Walbro relief valves disabled. With the car running the pumps get a steady 14-14.1V. I was already using gasoline as a test fluid, I wasn't brave enough to do it with the engine running.

I have tests showing 40, 50, 60, and 70psi with the battery charger on the low setting, and 50, 60, 70, 80, and 90 with it on the high setting. As I mentioned, without a good regulating power supply, as pressure goes up, voltage goes down and flow does as well, as expected.
Last edited by BlinkerFluid; 01-13-2011 at 06:05 PM.